Novel process for utilizing catalytic cracked heavy oil and condensed multinuclear anime prepared with same
A technology for catalytic cracking of heavy oil and aromatic resin, applied in the chemical field, can solve the problems of no synthesis of condensed polynuclear aromatic resin, resin curing, complex modification process, etc., and achieve good melt fluidity, excellent processing performance and simple process.
- Summary
- Abstract
- Description
- Claims
- Application Information
AI Technical Summary
Problems solved by technology
Method used
Image
Examples
Embodiment 1
[0042] 1. Add 1000Kg of catalytic cracking heavy oil into the enamel reaction kettle with heating jacket, and raise the temperature to 90°C;
[0043] 2. Start the mixer to stir at a speed of 90 rpm;
[0044] 3. Add 243Kg of tere-phenylenedimethanol as a linking agent at a molar ratio of 1:0.8 (catalytically cracked heavy oil: linking agent);
[0045] 4. Introduce 4 liters / min of nitrogen into the reactor;
[0046] 5, add mixed acid catalyst 62Kg by 5% of gross weight (weight ratio p-toluenesulfonic acid: hydrochloric acid=1: 0.5 mixes);
[0047] 6. The temperature of the reaction kettle is raised to 120°C for the reaction;
[0048] 7. After 6 hours of reaction, stop heating and settle for 1 hour;
[0049] 8. Separate the resin and unreacted oil in the lower part of the reactor;
[0050] 9, step 8 gained resin carries out solid-liquid extraction with 160# solvent naphtha;
[0051] 10. The resin obtained in step 9 is centrifuged, vacuum-dried, and ground to 200 meshes to ob...
Embodiment 2
[0055] 1. Put 1000Kg of catalytic cracking heavy oil into the enamel reaction kettle with heating jacket, and raise the temperature to 95°C;
[0056] 2. Start the mixer to stir at a speed of 95 rpm;
[0057] 3. Add linking agent paraformaldehyde 187Kg at a molar ratio of 1:1 (catalytic cracking heavy oil: linking agent);
[0058] 4. Introduce 4 liters / min of nitrogen into the reactor;
[0059] 5, add mixed acid catalyst 94.96Kg by 8% of gross weight (weight ratio p-toluenesulfonic acid: hydrochloric acid=1: 1.2 mixes);
[0060] 6. The temperature of the reaction kettle was raised to 125°C for the reaction;
[0061] 7. After reacting for 8 hours, stop heating and settle for 1 hour;
[0062] 8. Separate the resin and unreacted oil in the lower part of the reactor;
[0063] 9-11, the same as embodiment 1.
[0064] The obtained condensed polynuclear aromatic resin has a 10% thermal weight loss temperature of 390° C. after curing at 20 MPa and 151° C., a final carbonization yi...
Embodiment 3
[0066] 1. Put 1000Kg of catalytic cracking heavy oil into the enamel reaction kettle with heating jacket, and raise the temperature to 95°C;
[0067] 2. Start the mixer to stir at a speed of 100 rpm;
[0068] 3. Add linking agent paraformaldehyde 280Kg at a molar ratio of 1:1.5 (catalytically cracked heavy oil: linking agent);
[0069] 4. Into the reaction kettle, 6 liters / minute of nitrogen gas is introduced;
[0070] 5, add mixed acid catalyst 102Kg by 8% of gross weight (weight ratio p-toluenesulfonic acid: hydrochloric acid=1: 2 mixes);
[0071] 6. The temperature of the reaction kettle is raised to 150°C for the reaction;
[0072] 7. Stop heating after 10 hours of reaction, and settle for 1 hour;
[0073] 8. Separate the resin and unreacted oil in the lower part of the reactor;
[0074] 9-11 are identical with embodiment 1.
[0075] The obtained condensed polynuclear aromatic resin has a 10% thermal weight loss temperature of 415° C. after curing at 20 MPa and 160° C...
PUM
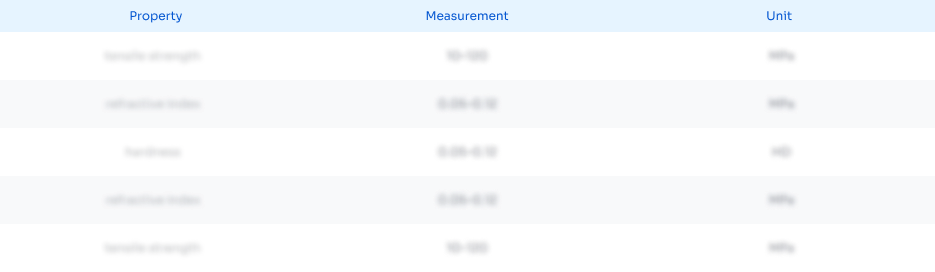
Abstract
Description
Claims
Application Information

- Generate Ideas
- Intellectual Property
- Life Sciences
- Materials
- Tech Scout
- Unparalleled Data Quality
- Higher Quality Content
- 60% Fewer Hallucinations
Browse by: Latest US Patents, China's latest patents, Technical Efficacy Thesaurus, Application Domain, Technology Topic, Popular Technical Reports.
© 2025 PatSnap. All rights reserved.Legal|Privacy policy|Modern Slavery Act Transparency Statement|Sitemap|About US| Contact US: help@patsnap.com