Synthesis method of low-molecular weight epoxy resin
A synthesis method and low molecular weight technology, applied in the direction of organic chemistry, can solve the problems of low epoxy value, large amount of waste water, high viscosity and other problems of liquid epoxy resin, and achieve fast reaction speed, extended production cycle and long reaction steps Effect
- Summary
- Abstract
- Description
- Claims
- Application Information
AI Technical Summary
Problems solved by technology
Method used
Image
Examples
preparation example Construction
[0028] The preparation embodiment of nano potassium carbonate:
[0029] Anhydrous low-carbon alcohol, such as absolute ethanol or absolute methanol, needs to be used in the preparation of nanopotassium carbonate, and its molar ratio to potassium hydroxide is 5~50:1.
[0030] Dissolve 0.3 mole of potassium hydroxide in 300ml of absolute ethanol with stirring, filter to remove insoluble mechanical impurities, put it into the reactor, feed carbon dioxide through the gas distributor, and carry out the reaction at 30°C. The progress of the reaction was monitored by acid-base titration. After the reaction of potassium hydroxide is complete, cool to 20°C. Filter, when the liquid is close to the solid liquid level (the solid must not be drained during the filtration process), wash the solid with cold absolute ethanol quickly until the moisture in the filtrate is lower than 0.1%, and immediately transfer the solid to absolute ethanol. 36g of nano-potassium carbonate was obtained, wit...
Embodiment 1
[0034] Add 1 mole of bisphenol A, 4 moles of epichlorohydrin, 2.5 moles of nano-potassium carbonate prepared by the above method and 70 ml of absolute ethanol into the reactor, raise the temperature to 60°C, and finish the reaction after 10 minutes. The reaction liquid is recovered by atmospheric distillation first. Ethanol, then vacuum distillation reclaims excessive epichlorohydrin, finally obtains bisphenol A type colorless low molecular weight liquid epoxy resin (342 grams), the product content of n=0 is greater than 90%, and epoxy value is 0.581.
Embodiment 2
[0036] Add 1 mole of bisphenol A, 10 moles of epichlorohydrin, 4 moles of nano-potassium carbonate prepared by the above method and 70 ml of anhydrous methanol into the reactor, and react at 20°C for 60 minutes. A small amount of epichlorohydrin was recovered by distillation to finally obtain bisphenol A type colorless low molecular weight liquid epoxy resin (340 grams), the product content of n=0 was greater than 90%, and the epoxy value was 0.580.
PUM
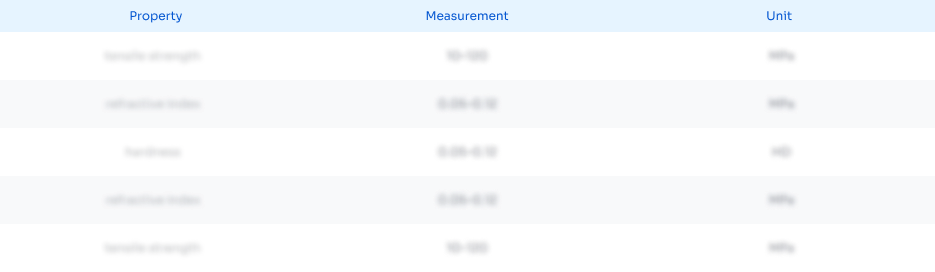
Abstract
Description
Claims
Application Information

- Generate Ideas
- Intellectual Property
- Life Sciences
- Materials
- Tech Scout
- Unparalleled Data Quality
- Higher Quality Content
- 60% Fewer Hallucinations
Browse by: Latest US Patents, China's latest patents, Technical Efficacy Thesaurus, Application Domain, Technology Topic, Popular Technical Reports.
© 2025 PatSnap. All rights reserved.Legal|Privacy policy|Modern Slavery Act Transparency Statement|Sitemap|About US| Contact US: help@patsnap.com