Method for decreasing harmful gases in process of sintering sintered neodymium iron boron (NdFeB) magnet
A sintering process and harmful gas technology, applied in the direction of magnetic objects, magnetic materials, electrical components, etc., can solve problems such as magnet blank cracks, affecting product qualification rate, surface coating blistering, etc., to reduce cracks and improve oxidation resistance , the effect of vacuum degree improvement
- Summary
- Abstract
- Description
- Claims
- Application Information
AI Technical Summary
Problems solved by technology
Method used
Image
Examples
Embodiment 1
[0025] The alloy with the composition of 9.7Pr-19Nd-4Dy-0.5Al-0.1Cu-1.2Co-1.0B-remainder Fe is smelted in a vacuum induction furnace to obtain a NdFeB alloy, which is subjected to hydrogen explosion treatment after coarse and medium crushing. Jet milling powder to obtain 3.7 ~ 4.0μm NdFeB alloy powder. The green compact size is D20×28. Place the dehydrogenation device in the sintering furnace, and place it inside the furnace body of the sintering furnace. Wherein, the dehydrogenation device is an airtight stainless steel box, in which is placed broken into 10 × 10 × 10mm 3 A small piece of LaNi5 hydrogen storage alloy activated by 99.99% high-purity hydrogen, and the device has a mechanical transmission to control the opening and closing of the box, wherein the hydrogen storage alloy occupies 1 / 3 of the volume of the box, and the top of the box to The distance between the molybdenum belts in the sintering furnace is 15cm. Put the green body into the sintering furnace for si...
Embodiment 2
[0027] The alloy with the composition of 10.3Pr-20Nd-4Dy-0.5Tb-0.2Gd-0.5Al-0.1Cu-1.2Co-1.2B-the balance of Fe is smelted in a vacuum induction furnace to obtain NdFeB alloy, after coarse and medium crushing The hydrogen explosion treatment is carried out, and the powder is obtained by jet milling to obtain 3.7-4.0 μm neodymium-iron-boron alloy powder. The green compact size is D20×28. Place the dehydrogenation device in the sintering furnace, and place it inside the furnace body of the sintering furnace. Wherein, the dehydrogenation device is an airtight stainless steel box, in which is placed broken into 10 × 10 × 10mm 3 A small piece of LaCeNi5 hydrogen storage alloy activated by 99.99% high-purity hydrogen, and the device has a mechanical transmission to control the opening and closing of the box, wherein the hydrogen storage alloy occupies 1 / 3 of the volume of the box, and the top of the box to The distance between the molybdenum belts in the sintering furnace is 15cm. ...
Embodiment 3
[0029] The alloy with the composition of 25.6Nd-2.4Dy-0.1Ga-0.9B-the balance of Fe is processed into thin strips by the thin strip process, and then hydrogen explosion treatment is carried out, and the powder is obtained by jet milling to obtain 3.7~4.0μm NdFeB alloy powder . The green compact size is D20×28. Place the dehydrogenation device in the sintering furnace, and place it inside the furnace body of the sintering furnace. Wherein, the dehydrogenation device is an airtight stainless steel box, in which is placed broken into 10 × 10 × 10mm 3 A small piece of LaCePrNi5 hydrogen storage alloy activated by 99.99% high-purity hydrogen, and the device has a mechanical transmission to control the opening and closing of the box, wherein the hydrogen storage alloy occupies 1 / 3 of the volume of the box, and the top of the box to The distance between the molybdenum belts in the sintering furnace is 15cm. Put the green body into a sintering furnace for sintering and aging. The si...
PUM
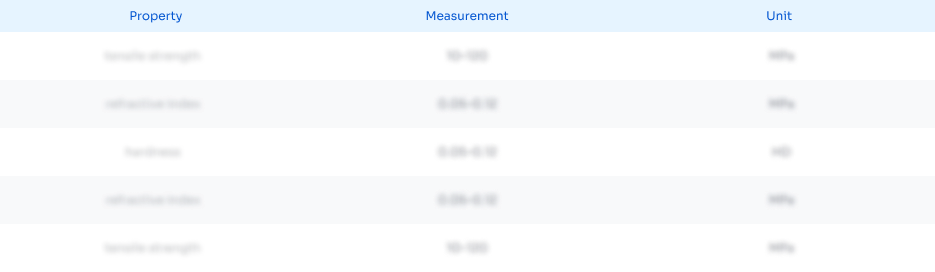
Abstract
Description
Claims
Application Information

- R&D
- Intellectual Property
- Life Sciences
- Materials
- Tech Scout
- Unparalleled Data Quality
- Higher Quality Content
- 60% Fewer Hallucinations
Browse by: Latest US Patents, China's latest patents, Technical Efficacy Thesaurus, Application Domain, Technology Topic, Popular Technical Reports.
© 2025 PatSnap. All rights reserved.Legal|Privacy policy|Modern Slavery Act Transparency Statement|Sitemap|About US| Contact US: help@patsnap.com