Method for preparing silicon nitride powder with low energy consumption and cost
A silicon nitride powder, low-cost technology, applied in the field of silicon nitride powder preparation, can solve the problems of long preparation time, long holding time, cost increase, etc., and achieve the effect of simple equipment, short preparation time and small investment
- Summary
- Abstract
- Description
- Claims
- Application Information
AI Technical Summary
Problems solved by technology
Method used
Examples
Embodiment Construction
[0009] The present invention will be described in detail below in conjunction with specific examples: the low-energy and low-cost silicon nitride powder preparation method of the present invention includes: the first is direct nitriding synthesis reaction, select 99.99% monocrystalline silicon powder powder as raw material , The raw material is calcined in the nitriding furnace at 1250 ± 5°C, and kept for 30-38h. The production environment of the reaction furnace is 99.999% nitrogen (N2), and the flow of N2 is controlled by a flow meter. The flow rate is 4L / min. The second is to perform post-treatments such as ball milling and pickling on the silicon nitride powder obtained by nitriding to obtain Si3N4 powder with a purity of up to 99.99%.
[0010] 1. Using the principle of silicon powder direct nitriding method to prepare silicon nitride powder (chemical reaction equation) as follows:
[0011] 3Si+2N 2 → Si 3 N 4
[0012] Nitriding synthesis reaction is carried out dire...
PUM
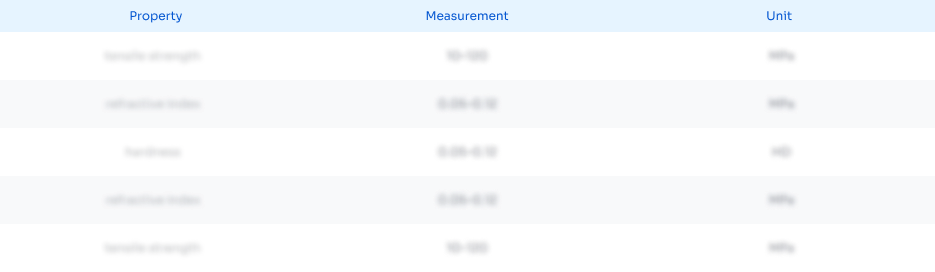
Abstract
Description
Claims
Application Information

- R&D Engineer
- R&D Manager
- IP Professional
- Industry Leading Data Capabilities
- Powerful AI technology
- Patent DNA Extraction
Browse by: Latest US Patents, China's latest patents, Technical Efficacy Thesaurus, Application Domain, Technology Topic, Popular Technical Reports.
© 2024 PatSnap. All rights reserved.Legal|Privacy policy|Modern Slavery Act Transparency Statement|Sitemap|About US| Contact US: help@patsnap.com