High-conductive heat-resistant aluminium alloy conductor and preparation method thereof
An aluminum alloy wire, high conductivity technology, applied in the direction of metal/alloy conductors, root rods/rods/wires/strip conductors, etc., can solve the problem of reducing the conductivity of aluminum alloys, reducing the heat resistance of aluminum alloys, and affecting heat-resistant aluminum alloys Transmission efficiency and other issues, to achieve the effect of high strength, high conductivity
- Summary
- Abstract
- Description
- Claims
- Application Information
AI Technical Summary
Problems solved by technology
Method used
Image
Examples
Embodiment 1
[0026] figure 1 It is a flow chart of the preparation of high-conductivity heat-resistant aluminum alloy wire, as shown in the figure, it is prepared according to the following steps:
[0027] 1. Preparation of master alloy: Take the preparation of Al-Zr alloy as an example to illustrate the preparation of master alloy. Metal Zr and 4N pure Al are weighed according to the proportion relationship that the Zr mass percentage content is 1%-3%. Put the weighed metal Zr into the feeding bin of the vacuum furnace, and then put 4N pure aluminum into the melting crucible of the vacuum furnace. After evacuating to 10-3Pa, backfill high-purity argon to the slight positive pressure in the vacuum furnace, and start to melt 4N pure aluminum. After the pure aluminum is melted, metal Zr is added to the aluminum melt through the feeding mechanism, and the metal Zr After the molten aluminum is melted and evenly mixed with the aluminum melt, the molten aluminum is poured into a high-purity mo...
Embodiment 2
[0037] Quote the alloy composition of Example 2 in Table 1, prepare according to the following steps:
[0038] 1. Prepare master alloy: prepare master alloy with the method of embodiment 1.
[0039] 2. Preparation of pure aluminum smelting and "boration" treatment: put 99.7% of the required pure aluminum into the melting furnace for smelting. Once the aluminum liquid appears in the melting furnace, add a conventional covering agent to prevent the aluminum liquid from oxidizing and absorbing gas. After the aluminum ingot is completely melted, raise the temperature to 880-900°C and keep it at this temperature for 30 minutes, then cool down the molten aluminum to 720°C, and remove the covering agent. Then add the weighed Al-B master alloy into the molten aluminum, and carry out "boration" treatment on the molten aluminum. After the Al-B intermediate is cleared, re-add the covering agent and raise the temperature of the aluminum liquid to 850°C and keep it warm for 40 minutes. T...
PUM
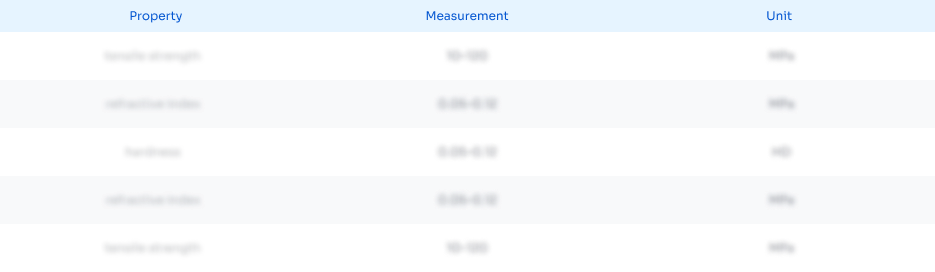
Abstract
Description
Claims
Application Information

- R&D
- Intellectual Property
- Life Sciences
- Materials
- Tech Scout
- Unparalleled Data Quality
- Higher Quality Content
- 60% Fewer Hallucinations
Browse by: Latest US Patents, China's latest patents, Technical Efficacy Thesaurus, Application Domain, Technology Topic, Popular Technical Reports.
© 2025 PatSnap. All rights reserved.Legal|Privacy policy|Modern Slavery Act Transparency Statement|Sitemap|About US| Contact US: help@patsnap.com