Natural polymer film material with adjustable degradation rate and preparation method
A natural polymer and film material technology, applied in the field of green and environment-friendly polymer film materials, can solve the problems of uncontrollable degradation rate, film without antibacterial or antibacterial components, high processing cost, etc., to achieve economic value and practical value, The effect of increasing the concentration range of the glue solution and reducing the processing cost
- Summary
- Abstract
- Description
- Claims
- Application Information
AI Technical Summary
Problems solved by technology
Method used
Examples
preparation example Construction
[0022]A method for preparing a natural polymer film material with an adjustable degradation rate. The components and mass percentages of the film material are: 35-50% starch, 5-30% konjac powder, 0.1-5% glycerin, and 15-60% modified additives %; it is characterized in that: the components included in the modified additive and the percentage of the total mass of the membrane material are: 5% to 55% of water, 5 to 10% of lactic acid, and 0.001 to 1 %, the preparation method of the film material is: mixing-microwave-casting-setting process; the water content is 5% to 55%, and the specific value is related to the drying process during preparation and the air humidity during use; the characteristics of starch Yes: at least one of natural starch and soluble starch; wherein the characteristic of natural starch is: it is pure natural starch without any modification treatment, extracted from one of potato, cassava, pea, corn, or sweet potato; Among them, the characteristics of konjac p...
Embodiment 1
[0033] Example 1: dilute 50ml lactic acid with 2000ml water, add dilute lactic acid solution after mixing 30g potato starch and 20g konjac powder, add 20ml glycerin after stirring for 10 minutes, and stir for 5 minutes; the above-mentioned mixed glue is heated to boiling by microwave 5 minutes; filter (200 mesh), place under a negative pressure of 400-500 mm Hg for defoaming; stir and preheat to 70 ° C, evenly distribute on the casting plate through the nozzle of the casting equipment, and dry at 90 ° C film; then above-mentioned casting film is soaked in the sizing agent (25% concentration ammonia water and 99.7% concentration ethanol are mixed and prepared by volume ratio 1:5) solution for 12 hours, rinse 3 times with clear water (each soaking 30 minutes), After drying, the natural polymer film material with adjustable degradation rate can be obtained (the water content reaches 5% to 55%, and the specific value is related to the drying process and air humidity).
Embodiment 2
[0034] Embodiment 2: Dilute 40ml lactic acid with 2000ml water, add dilute lactic acid solution after mixing 40g cornstarch and 15g konjac fine powder, add 30ml glycerin after stirring for 10 minutes, stir for 5 minutes again; Above-mentioned mixed glue is carried out microwave heating to boiling 5 minutes; filter (200 mesh), place under a negative pressure of 400-500 mm Hg for defoaming; stir and preheat to 70 ° C, evenly distribute on the casting plate through the nozzle of the casting equipment, and dry at 90 ° C film; then above-mentioned casting film is soaked in the sizing agent (25% concentration ammonia water and 99.7% concentration ethanol are mixed and prepared by volume ratio 1:5) solution for 12 hours, rinse 3 times with clear water (each soaking 30 minutes), After drying, the natural polymer film material with adjustable degradation rate can be obtained (the water content reaches 5% to 55%, and the specific value is related to the drying process and air humidity). ...
PUM
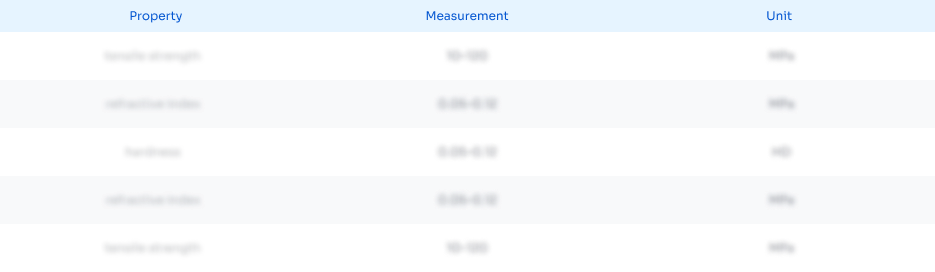
Abstract
Description
Claims
Application Information

- R&D
- Intellectual Property
- Life Sciences
- Materials
- Tech Scout
- Unparalleled Data Quality
- Higher Quality Content
- 60% Fewer Hallucinations
Browse by: Latest US Patents, China's latest patents, Technical Efficacy Thesaurus, Application Domain, Technology Topic, Popular Technical Reports.
© 2025 PatSnap. All rights reserved.Legal|Privacy policy|Modern Slavery Act Transparency Statement|Sitemap|About US| Contact US: help@patsnap.com