Method for preparing cyclopentanol from cyclopentene through hydration
A technology composed of cyclopentene water and cyclopentene water, applied in hydroxyl addition preparation, organic chemistry and other directions, can solve the problems of high toxicity of phenol, difficult stirring, high viscosity, etc., to improve the reaction yield and increase mutual solubility. , the effect of reducing energy consumption
- Summary
- Abstract
- Description
- Claims
- Application Information
AI Technical Summary
Problems solved by technology
Method used
Examples
Embodiment 1
[0015] The hydration reaction is carried out in a 250ml autoclave with a heating device and a stirring device in the autoclave. Add 43.20g H to the autoclave 2 O (2.40mol), 27.20g n-butanol, 9.66g Amberlyst36 resin catalyst, 27.20g (0.4mol) cyclopentene, replace the air in the system with nitrogen three times, boost the pressure to 1.20MPa, stir and heat up, and control the reaction temperature at 120 ~160°C, the reaction time is 4h.
[0016] After the reaction is finished, cool to room temperature, discharge the material, filter the resin with a 90-mesh standard sieve, separate the reaction liquid, and distill and separate the water phase material and the oil phase material respectively to obtain cyclopentanol and unreacted cyclopentene.
Embodiment 2
[0024] In a high-pressure vessel, water, cyclopentene and n-butanol are added in a molar ratio of 4:1. The mass ratio of n-butanol to cyclopentene is 1:1. Next, replace the air in the system with nitrogen for 3 times, increase the pressure to 1.0Mpa, and react for 8 hours at 120°C to obtain cyclopentanol. The amount of acidic cation exchange resin Amberlyst35 is 9% of the total mass of the system. The conversion rate of cyclopentene was 14.56%, and the selectivity of cyclopentanol was 90.48%.
Embodiment 3
[0026] In a high-pressure vessel, water, cyclopentene and n-pentanol are added in a molar ratio of 6:1. The mass ratio of n-pentanol to cyclopentene is 2:1. After replacing the air in the system twice with nitrogen, the pressure was increased to 3.0Mpa, and the reaction was carried out at 160°C for 0.5h to obtain cyclopentanol. The amount of acidic cation exchange resin Amberlyst15 is 9% of the total mass of the system. The conversion rate of cyclopentene was 25.20%, and the selectivity of cyclopentanol was 58.70%.
PUM
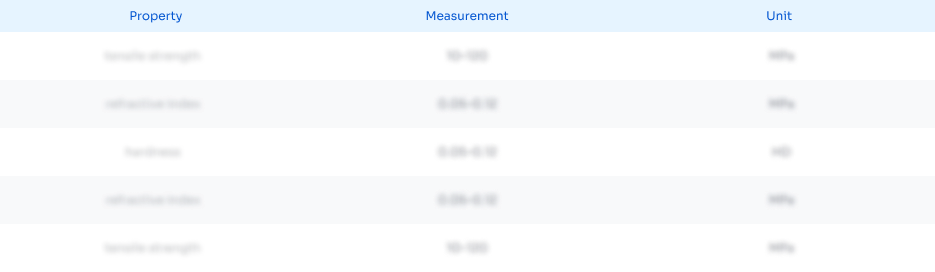
Abstract
Description
Claims
Application Information

- R&D
- Intellectual Property
- Life Sciences
- Materials
- Tech Scout
- Unparalleled Data Quality
- Higher Quality Content
- 60% Fewer Hallucinations
Browse by: Latest US Patents, China's latest patents, Technical Efficacy Thesaurus, Application Domain, Technology Topic, Popular Technical Reports.
© 2025 PatSnap. All rights reserved.Legal|Privacy policy|Modern Slavery Act Transparency Statement|Sitemap|About US| Contact US: help@patsnap.com