Soldering flux and preparation method thereof
A flux and wetting agent technology, which is applied in welding equipment, welding medium, manufacturing tools, etc., can solve the problems that affect the service life of copper-aluminum composite pipe, reduce the tensile strength of the weld, affect the appearance of the product, and damage the reliability, etc., to achieve Improve welding effect, strong manufacturability, and good air tightness
- Summary
- Abstract
- Description
- Claims
- Application Information
AI Technical Summary
Problems solved by technology
Method used
Examples
Embodiment 1
[0025] The composition of the flux is by weight percentage, respectively:
[0026] Water White Hydrogenated Rosin 96.39%
[0027] Polyacrylic resin 0.15%
[0028] Malonic acid 0.4%
[0029] Adipic acid 1.0%
[0030] Cyclohexylamine hydrochloride 1.6%
[0031] Dibromoethylbenzene 0.3%
[0032] FC-135 0.1%
[0033] Tetrazole 0.06%
[0034] Preparation:
[0035] Accurately weigh the reagents and rosin required for the above-mentioned flux according to the requirements of the flux formula ratio, add the compounded rosin in proportion to the reaction kettle with heating function, heat to 110°C, and mix it evenly; slowly Raise the temperature to 140°C, add organic acid activator, wetting agent, surfactant and corrosion inhibitor in proportion at this temperature, and stir for 0.5h; pour the prepared flux into the tin wire with heat preservation function and extrude machine rosin barrels to obtain finished products.
Embodiment 2
[0037] The composition of the flux is by weight percentage, respectively:
[0038] Water White Hydrogenated Rosin 70%
[0039] Dipolymerized Rosin 25.1%
[0040] Malonic acid 0.6%
[0041] Glutaric acid 1.0%
[0042] Dibromoethylamine hydrobromide 1.8%
[0043] FSN-100 0.5%
[0044] Ethylene Glycol Benzazole 0.1%
[0045] Preparation:
[0046]Accurately weigh the reagents and rosin required for the above-mentioned flux according to the requirements of the flux formula ratio, add the compounded rosin in proportion to the reaction kettle with heating function, heat to 110°C, and mix it evenly; slowly Raise the temperature to 140°C, add organic acid activator, wetting agent, surfactant and corrosion inhibitor in proportion at this temperature, and stir for 0.5h; pour the prepared flux into the tin wire with heat preservation function and extrude machine rosin barrels to obtain finished products.
Embodiment 3
[0048] The composition of the flux is by weight percentage, respectively:
[0049] Water White Hydrogenated Rosin 50%
[0050] Dipolymer Rosin 30%
[0051] Disproportionated Rosin 17.04%
[0052] Malonic acid 0.3%
[0053] Succinic Acid 0.6%
[0054] Glutaric acid 1.0%
[0055] Aniline 0.6%
[0056] Diethanolamine 0.2%
[0057] OP-6 0.2%
[0058] Tetrazole 0.06%
[0059] Preparation:
[0060] Accurately weigh the reagents and rosin required for the above-mentioned flux according to the requirements of the flux formula ratio, add the compounded rosin in proportion to the reaction kettle with heating function, heat to 110°C, and mix it evenly; slowly Raise the temperature to 140°C, add organic acid activator, wetting agent, surfactant and corrosion inhibitor in proportion at this temperature, and stir for 0.5h; pour the prepared flux into the tin wire with heat preservation function and extrude machine rosin barrels to obtain finished products.
PUM
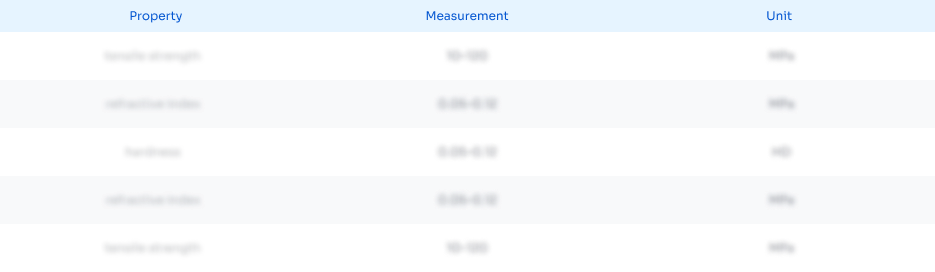
Abstract
Description
Claims
Application Information

- R&D
- Intellectual Property
- Life Sciences
- Materials
- Tech Scout
- Unparalleled Data Quality
- Higher Quality Content
- 60% Fewer Hallucinations
Browse by: Latest US Patents, China's latest patents, Technical Efficacy Thesaurus, Application Domain, Technology Topic, Popular Technical Reports.
© 2025 PatSnap. All rights reserved.Legal|Privacy policy|Modern Slavery Act Transparency Statement|Sitemap|About US| Contact US: help@patsnap.com