Process for preparing ascorbic acid ester
An ascorbic acid and process technology, applied in the field of preparation of ascorbic acid esters, can solve problems such as increased post-processing difficulty, reduced product yield, and difficulty in suction filtration, and can avoid excessive drying time, reduce the content of impurities, and avoid the reduction of purity. Effect
- Summary
- Abstract
- Description
- Claims
- Application Information
AI Technical Summary
Problems solved by technology
Method used
Examples
Embodiment 1
[0034] ①Put 648.0g of palmitic acid into the reaction kettle, slowly add 3.2kg of 95% concentrated sulfuric acid and stir until it is molten (about 20min), then add 300.0g of ascorbic acid, and continue to stir and react for 18h at 20°C to 25°C;
[0035] ②Reduce the temperature of the reaction mixture in step ① to 5°C, slowly add 1.4kg of water at 0°C to 4°C until the temperature of the mixture no longer rises, then add 2.8kg of room temperature water to dilute the mixture, then add 3.1kg of acetone and 7.7kg For the mixed solution of chloroform, heat up to 30°C, stir and extract for 20 minutes; separate and remove the aqueous phase;
[0036] ③Add water at 25°C to the mixed liquid phase of chloroform and acetone obtained in step ②, the amount of water added each time is 4.2kg, stir and wash until the pH value is 6.5; separate and remove the water phase; wash to hydrolyze the sulfuric acid ester and remove sulfuric acid and water-soluble sex impurities;
[0037] ④The mixed org...
Embodiment 2
[0040] ①Put 3.15kg of sodium palmitate into the reactor, slowly add 37.8kg of 95% concentrated sulfuric acid and stir until molten (about 20min), then add 2.1kg of sodium ascorbate, and continue to stir and react for 24h at 20°C to 25°C;
[0041] ②Reduce the temperature of the reaction mixture in step ① to 15°C, slowly add 29.5kg of water at 0°C to 4°C until the temperature of the mixture no longer rises, then add 56.6kg of room temperature water to dilute the mixture, then add 77.5kg of methyl ethyl ketone and 309.5 kg of dichloroethane mixture, heated to 35°C, stirred and extracted for 30 minutes; separated and removed the water phase;
[0042] ③ Add water at 30°C to the mixed liquid phase of butanone and dichloroethane obtained in step ②, stir and wash until the pH value is 7.0; separate and remove the water phase; wash to hydrolyze the sulfuric acid ester and remove sulfuric acid and water-soluble impurities;
[0043] ④The mixed organic phase obtained in step ③ was subject...
Embodiment 3
[0046] ①Put 3kg of cinnamic acid into the reaction kettle, slowly add 30kg of 98% concentrated sulfuric acid and stir until it reaches a molten state (about 20min), then add 3kg of ascorbic acid, and continue to stir and react for 22h at 20°C to 25°C;
[0047] ② Cool down the reaction mixture in step ① to 25°C, slowly add 150kg of water until the temperature of the mixture no longer rises, then add 210kg of room temperature water to dilute the mixture, then add a mixed solution of 39.6kg of butyraldehyde and 356.4kg of tribromomethane, Heat up to 50°C, stir and extract for 40 minutes; separate and remove the water phase;
[0048] ③Add 35°C water to the mixed liquid phase of butyraldehyde and tribromomethane obtained in step ②, stir and wash until the pH value is 5.5; separate and remove the water phase; wash to hydrolyze the sulfuric acid ester and remove sulfuric acid and water-soluble impurities;
[0049] ④The mixed organic phase obtained in step ③ was subjected to vacuum di...
PUM
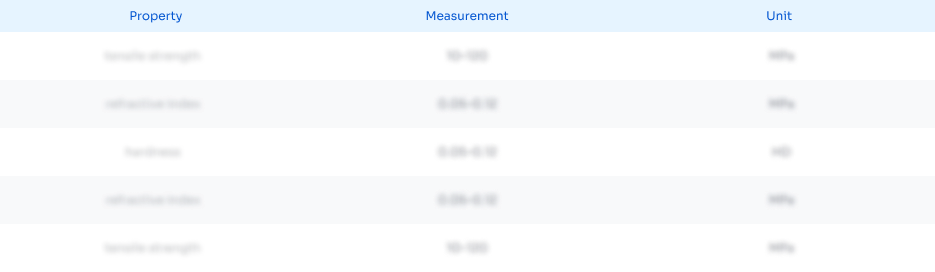
Abstract
Description
Claims
Application Information

- Generate Ideas
- Intellectual Property
- Life Sciences
- Materials
- Tech Scout
- Unparalleled Data Quality
- Higher Quality Content
- 60% Fewer Hallucinations
Browse by: Latest US Patents, China's latest patents, Technical Efficacy Thesaurus, Application Domain, Technology Topic, Popular Technical Reports.
© 2025 PatSnap. All rights reserved.Legal|Privacy policy|Modern Slavery Act Transparency Statement|Sitemap|About US| Contact US: help@patsnap.com