Electric power-assisted steering system with VTMS (Variable Transmission Motor System) speed variable transmission ratio
An electric power steering and variable transmission ratio technology, applied in electric steering mechanism, mechanical steering gear, electric components, etc., can solve the problems of high assembly and manufacturing precision, complex system mechanism, cumbersome control algorithm, etc., to improve safety, speed change, etc. The process is simple and the effect of the mechanical transmission system is omitted
- Summary
- Abstract
- Description
- Claims
- Application Information
AI Technical Summary
Problems solved by technology
Method used
Image
Examples
Embodiment 1
[0029] In embodiment one:
[0030] When it is detected that the wheel speed signal 19 is 0 or the speed is very low, turn the steering wheel 1, the motor stator winding 22 rotates in opposite directions around the permanent magnet rotor 23, the output of the motor angle signal 13 is a forward speed signal, and the wheel speed signal 19 gradually changes. small, the motor stator winding 22 rotates in opposite directions around the permanent magnet rotor 23, and the speed of the motor stator winding 22 gradually increases, the output speed signal of the motor angle signal 13 also becomes higher, and at the same time, the angular transmission ratio of the steering system decreases, and the steering becomes more and more The more direct, the less steering travel, making the steering more responsive in situ and at low speeds.
Embodiment 2
[0031] In the second embodiment:
[0032] When it is detected that the wheel speed signal 19 is at a high speed, the steering wheel 1 is rotated, and the motor stator winding 22 rotates in the opposite direction around the permanent magnet rotor 23. The rotational speed of the winding 22 around the permanent magnet rotor 23 is also gradually increased, and the output rotational speed signal of the motor angle signal 13 is enhanced. At the same time, the angular transmission ratio of the steering system is getting larger and larger, and the steering is more indirect, so that the steering of the car at high speed is more stable and improves the speed. Car driving safety.
Embodiment 3
[0033] In embodiment three:
[0034] When it is detected that the wheel speed signal 19 is at a medium speed, turn the steering wheel 1, the motor stator winding 22 is relatively stationary around the permanent magnet rotor 23, the VTMS 5 is in a locked-rotor state, the output of the motor angle signal 13 is about 0, and the VTMS 5 does not turn. It is gear changing function; when VTMS 5 breaks down, the relay 27 pushes the clutch 26 to engage, and the steering action is transmitted from the intermediate transmission shaft 4 to the output shaft 25. The entire steering system will not have the function of variable transmission ratio, but the steering system can still work .
PUM
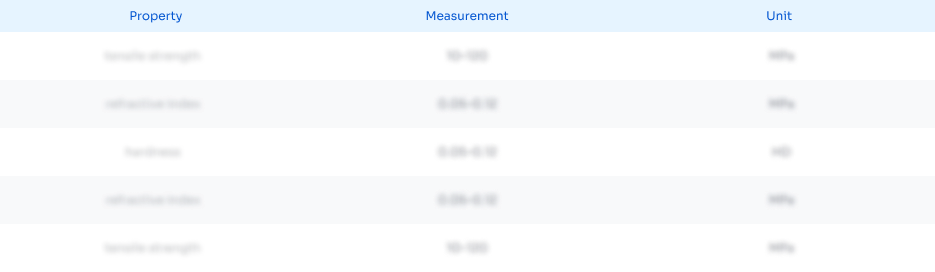
Abstract
Description
Claims
Application Information

- R&D
- Intellectual Property
- Life Sciences
- Materials
- Tech Scout
- Unparalleled Data Quality
- Higher Quality Content
- 60% Fewer Hallucinations
Browse by: Latest US Patents, China's latest patents, Technical Efficacy Thesaurus, Application Domain, Technology Topic, Popular Technical Reports.
© 2025 PatSnap. All rights reserved.Legal|Privacy policy|Modern Slavery Act Transparency Statement|Sitemap|About US| Contact US: help@patsnap.com