Formulation of a metalworking fluid
A metal processing and fluid technology, applied in the petroleum industry, base materials, lubricating compositions, etc., can solve the problems of expensive, difficult maintenance, lack of protective barrier film, etc.
- Summary
- Abstract
- Description
- Claims
- Application Information
AI Technical Summary
Problems solved by technology
Method used
Image
Examples
Embodiment 1
[0077] Table 1
[0078]
[0079] Materials A-E of Table 1 were used in a tapping torque operation involving the tapping of 6061 aluminum. The concentrate was first diluted to a 7.5% by volume solution prior to testing. The tapping torque test is a quantitative measure of the lubricity of a metalworking fluid. Its ASTM standard method name is D5619. Tapping torque reflects the industrial machining process better than other tests, which are usually performed by rubbing two metal surfaces together. It is an excellent method for identifying the machinability of metalworking fluid (MWF) products in the laboratory. Tapping torque results have been shown to be closely related to field machinability.
[0080] The Tapping Torque Tester is designed to measure the lubricity of MWF while actually cutting. During the tapping operation, the tapping torque meter measured 250 momentary torques as the tap advanced through the depth of cut. Specialized software then facilitates the ana...
Embodiment 2
[0086] The materials of Table 1 were used in particle size operations involving the measurement of volume average particle size in nanometers. The concentrate was first diluted to a 7.5% by volume solution with water prior to testing. Particle-sizing instruments use high-efficiency dynamic light scattering to quantify particle sizes from 20-100,000 nanometers.
[0087] All samples were diluted to 7.5% by volume prior to testing. The resulting particle sizes are shown in Table 1.
Embodiment 3
[0089] Material C of Table 1 was tested for particle size at two different concentrations and evaluated for appearance and emulsion stability at each concentration. The results are presented in Table 2, which showed large average particle size, opaque appearance and excellent stability at each concentration. Larger particle sizes are characteristic of better lubricants. Typical synthetic MWFs form clear solutions on dilution with particle sizes less than 100 nm. Diluted sample C had a particle size 3.5-20 times larger than the largest size observed for typical synthetic MWFs.
[0090] Table 2
[0091]
[0092]
[0093] From Examples 1-3 it can be seen that the best lubricity and particle size was obtained with Sample C, which incorporated 10% carboxylic acid-alkali salt and 20% Pluronic "R" block Copolymers combined. This ratio results in maximum volume average particle size and maximum lubricity.
[0094] It is also evident from this example that the lubricity of t...
PUM
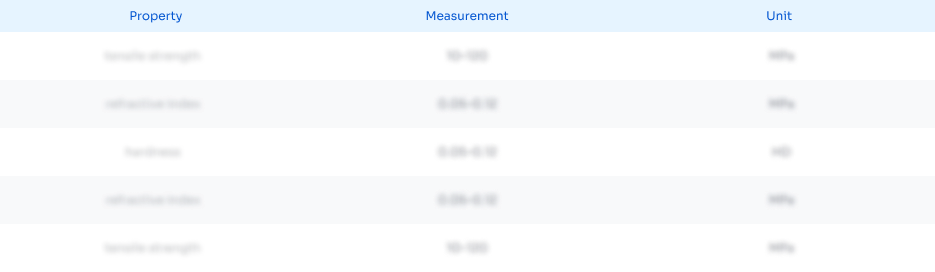
Abstract
Description
Claims
Application Information

- R&D
- Intellectual Property
- Life Sciences
- Materials
- Tech Scout
- Unparalleled Data Quality
- Higher Quality Content
- 60% Fewer Hallucinations
Browse by: Latest US Patents, China's latest patents, Technical Efficacy Thesaurus, Application Domain, Technology Topic, Popular Technical Reports.
© 2025 PatSnap. All rights reserved.Legal|Privacy policy|Modern Slavery Act Transparency Statement|Sitemap|About US| Contact US: help@patsnap.com