Hot rolling heating method for low-carbon aluminum killed steel casting blank
A technology of low carbon aluminum killed steel and heating method, which is applied in the field of hot rolling and heating of low carbon aluminum killed steel casting billets, can solve the problems of reducing yield, oxidation burning loss, shortening life, etc., and achieves good surface quality and mechanical properties. Stable, uniformity-improving effect
- Summary
- Abstract
- Description
- Claims
- Application Information
AI Technical Summary
Problems solved by technology
Method used
Image
Examples
Embodiment 1
[0024] The hot-rolled steel coils are steel coils with a number of 1 to 6, the steel is St12, and its chemical composition is shown in Table 1. The rolling specification is 3.25×1050mm. ℃), the total heating time is 140-142min, and the furnace temperature and total heating time of the preheating section, heating section and soaking section are shown in Table 2. The rolling temperature is 868-887°C, and the properties of the finished product are shown in Table 3.
[0025] Table 1
[0026]
[0027] Table 2
[0028]
[0029] table 3
[0030]
[0031] As can be seen from Table 2 and Table 3, the steel coils whose hot-rolled steel coil numbers are 1 to 6 in Embodiment 1 are controlled at a heating temperature between 1170 and 1193° C. (average 1181.5° C.), and the total heating time is 140 ~142min, the product performance fully meets the standard requirements. Embodiment 1 Compared with the original method, the average heating temperature is reduced by 19.5° C., and th...
Embodiment 2
[0033] The hot-rolled steel coils are 7-11 steel coils, the steel quality is DX51D+Z, the chemical composition content is shown in Table 4, the rolling specification is 2.5×1050mm, the slab is cold-charged, and the slab exit temperature is 1163-1168°C ( average 1165.5°C), heating time 140-147min, the furnace temperature and total heating time of the preheating section, heating section and soaking section are shown in Table 5, after heating, hot continuous rolling rough rolling 5 passes, low carbon aluminum killed steel The final rolling temperature is 853-869°C, and the performance of the finished product is shown in Table 6.
[0034] Table 4
[0035]
[0036] table 5
[0037]
[0038] Table 6
[0039]
[0040] It can be seen from Table 5 and Table 6 that the heating temperature of the hot-rolled steel coils of Example 2 whose numbers are 7-11 is controlled at 1163-1168°C (1165.5°C on average), and the total heating time is 140-147min , Tracking product performance...
Embodiment 3
[0042] The hot-rolled steel coils are 12-18 steel coils, the steel is St13, the chemical composition content is shown in Table 7, the rolling specification is 3.25×1050mm, the billet is hot-charged at 575-615°C, and the billet exit temperature is 1167-1188 ℃ (average 1176.8 ℃), the total heating time is 137-143min, the furnace temperature and total heating time of the preheating section, heating section and soaking section are shown in Table 8, after heating, hot continuous rolling rough rolling 5 passes, low carbon The final rolling temperature of aluminum-killed steel is 871-890°C, and the properties of the finished product are shown in Table 9.
[0043] Table 7
[0044]
[0045] Table 8
[0046]
[0047] Table 9
[0048]
[0049] It can be seen from Table 8 and Table 9 that the heating temperature of the hot-rolled steel coils in Example 1 with the number 12-18 is controlled at 1167-1188°C (1176.8°C on average), and the total heating time is 137-143min , the pro...
PUM
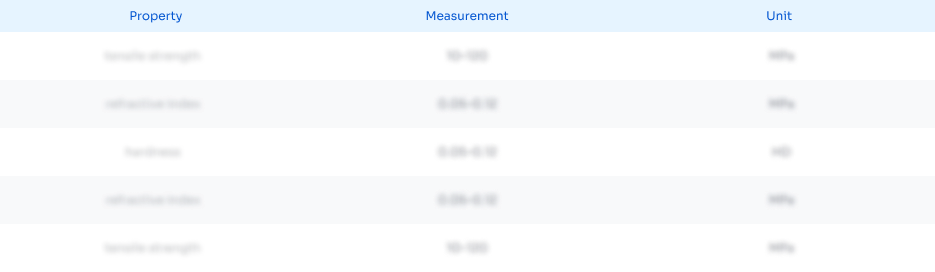
Abstract
Description
Claims
Application Information

- R&D
- Intellectual Property
- Life Sciences
- Materials
- Tech Scout
- Unparalleled Data Quality
- Higher Quality Content
- 60% Fewer Hallucinations
Browse by: Latest US Patents, China's latest patents, Technical Efficacy Thesaurus, Application Domain, Technology Topic, Popular Technical Reports.
© 2025 PatSnap. All rights reserved.Legal|Privacy policy|Modern Slavery Act Transparency Statement|Sitemap|About US| Contact US: help@patsnap.com