Cold heading extrusion forming processing method for shaft sleeve of clutch shaft of impeller type full-automatic washing machine
A technology of a fully automatic washing machine and a processing method, which is applied to washing machines with containers, metal processing equipment, washing devices, etc., can solve the problems of reducing the mechanical properties of parts, work efficiency, and high manufacturing costs, and improve The effect of saving raw materials and reducing cutting allowance
- Summary
- Abstract
- Description
- Claims
- Application Information
AI Technical Summary
Problems solved by technology
Method used
Image
Examples
Embodiment Construction
[0019] The present invention will be further described below in conjunction with the drawings and embodiments.
[0020] Such as Figure 1 to Figure 6 As shown, the cold heading extrusion forming method of the clutch shaft sleeve of the pulsator-type automatic washing machine, the shaft sleeve 1 includes a shaft sleeve 2 and a base 3 arranged at the bottom end of the shaft sleeve 2, and the shaft sleeve 2 and the base 3 are formed Integral shape, and the inner cavity 4 of the shaft sleeve 2 is communicated with the base 3. The cold heading extrusion forming method of the sleeve 1 is as follows:
[0021] Step 1. Prepare the cylindrical blank 5 according to the design requirements for use;
[0022] Step two, feed the blank into the first mold 6, according to the set requirements, one end is upset and chamfered, the upsetting rod 7 upsets a counterbore in the middle of the blank end surface in a vertical direction, and the middle part of the inner chamfer plane is fixed with another On...
PUM
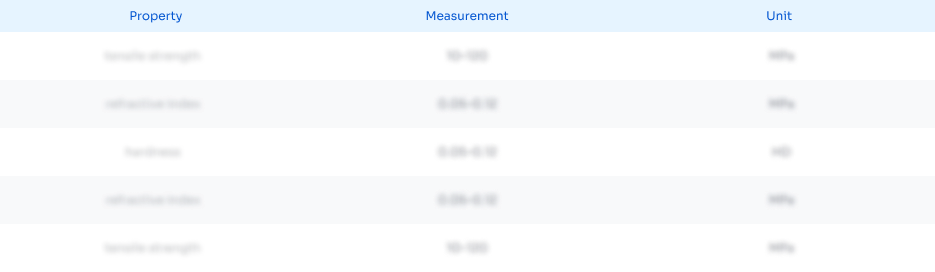
Abstract
Description
Claims
Application Information

- Generate Ideas
- Intellectual Property
- Life Sciences
- Materials
- Tech Scout
- Unparalleled Data Quality
- Higher Quality Content
- 60% Fewer Hallucinations
Browse by: Latest US Patents, China's latest patents, Technical Efficacy Thesaurus, Application Domain, Technology Topic, Popular Technical Reports.
© 2025 PatSnap. All rights reserved.Legal|Privacy policy|Modern Slavery Act Transparency Statement|Sitemap|About US| Contact US: help@patsnap.com