Preparation method of titanium dioxide film grown in situ on surface of titanium or titanium alloy material
A technology of titanium dioxide and in-situ growth, which is applied to the surface modification of titanium and titanium alloy materials. In the field of surface modification of titanium and titanium alloy materials, ion plasma technology can solve the problems of weak matrix binding force, influence by electrolyte, small film thickness, etc. problems, to achieve good binding, good photocatalytic or photocatalytic activity, and short time-consuming effects
- Summary
- Abstract
- Description
- Claims
- Application Information
AI Technical Summary
Problems solved by technology
Method used
Examples
Embodiment 1
[0026] This embodiment is a method for growing a titanium dioxide film in situ on a titanium surface by using a titanium material as an anode, comprising the following steps:
[0027] (1) Pretreatment of titanium material surface: Ultrasonic cleaning in deionized water for 10 minutes, pickling in acid solution at 49°C for 1 minute after removing water, and finally ultrasonic cleaning in deionized water for 5 minutes, drying in a vacuum oven The acid solution is composed of: 30% nitric acid (70%)+3% hydrofluoric acid (60%), wherein the volume ratio of nitric acid and hydrofluoric acid is 10:1;
[0028] (2) Put the pretreated titanium material into the high-voltage pulse discharge reactor, use the titanium material as the anode of the high-voltage electrode, and use the multi-needle electrode as the cathode (grounding electrode);
[0029] (3) The distance between the electrodes is 100mm, oxygen is introduced, and the flow rate of oxygen is 0.5m 3 / h;
[0030] (4) Turn on the hig...
Embodiment 2
[0033] This embodiment is a method for growing a titanium dioxide film in situ on the surface of a titanium alloy material using a titanium alloy as an anode and a cathode, including the following steps:
[0034] (1) Pretreatment of the surface of titanium alloy materials: Ultrasonic cleaning in deionized water for 10 minutes, after removing water, pickling in acid solution at 49°C for 4 minutes, finally ultrasonic cleaning in deionized water for 5 minutes, and drying in a vacuum oven Stand-by, the acid composition is: 20% nitric acid (70%)+2% hydrofluoric acid (60%), wherein the volume ratio of nitric acid and hydrofluoric acid is 10:1;
[0035] (2) Put the two pretreated titanium alloy materials as the anode and cathode of the high-voltage electrode respectively, and put them into the high-voltage pulse discharge reactor;
[0036] (3) The distance between the electrodes is 5mm, oxygen is introduced, and the flow rate of oxygen is 0.4m 3 / h;
[0037] (4) Apply positive and ...
Embodiment 3
[0040] This embodiment is a method for using a porous titanium alloy as an anode to grow a titanium dioxide film in situ on the surface of a porous titanium alloy material, including the following steps:
[0041] (1) Pretreatment of the surface of the porous titanium alloy material: Ultrasonic cleaning in deionized water for 20 minutes, pickling in acid solution at 49°C for 10 minutes after removing moisture, and finally ultrasonic cleaning in deionized water for 10 minutes, and drying in a vacuum oven Dry for use, the composition of the acid solution is: 10% nitric acid (70%) + 1% hydrofluoric acid (60%), wherein the volume ratio of nitric acid and hydrofluoric acid is 10:1;
[0042] (2) Put the pretreated porous titanium alloy material into a high-voltage pulse discharge reactor, use the porous titanium alloy material as the anode of the high-voltage electrode, and use the multi-needle stainless steel electrode as the cathode (grounding electrode);
[0043] (3) The distance ...
PUM
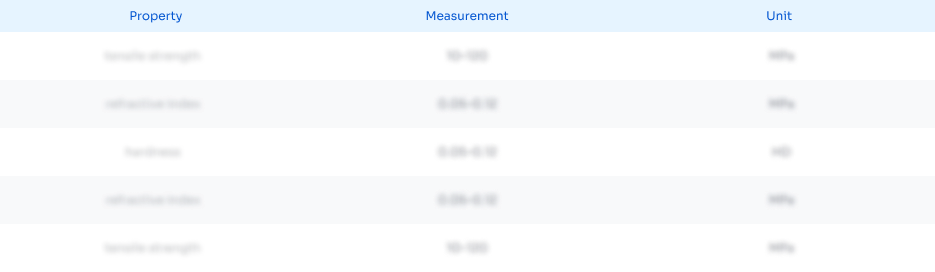
Abstract
Description
Claims
Application Information

- Generate Ideas
- Intellectual Property
- Life Sciences
- Materials
- Tech Scout
- Unparalleled Data Quality
- Higher Quality Content
- 60% Fewer Hallucinations
Browse by: Latest US Patents, China's latest patents, Technical Efficacy Thesaurus, Application Domain, Technology Topic, Popular Technical Reports.
© 2025 PatSnap. All rights reserved.Legal|Privacy policy|Modern Slavery Act Transparency Statement|Sitemap|About US| Contact US: help@patsnap.com