Device and method for breakout prediction during slab continuous casting
A slab continuous casting and breakout technology, which is applied in the configuration of indicating equipment/measuring equipment, casting equipment, manufacturing tools, etc., can solve the problem that cracks and breakouts are difficult to catch, cannot display mold copper plates dynamically in real time, and calculate speed Can not meet the real-time calculation and display requirements of continuous casting production and other issues
- Summary
- Abstract
- Description
- Claims
- Application Information
AI Technical Summary
Problems solved by technology
Method used
Image
Examples
Embodiment Construction
[0015] The invention discloses a device for predicting steel breakout in the slab continuous casting process, such as figure 1 As shown, the side wall of the crystallizer is composed of the west side 101, the east side 102, the outer arc 103 and the inner arc 104 of the surrounding mold, on the side wall of the continuous casting mold from the meniscus of the mold to the outlet of the mold in an array At least 4 rows of thermocouples 200 are arranged in the form of the thermocouples, and the thermocouples are all connected to a calculation control unit, and the calculation control unit calculates the temperature distribution of the molten steel in the crystallizer according to the temperature information of the thermocouples, so as to determine whether leakage is required. Steel alarm.
[0016] At least one row of thermocouples is respectively arranged on the meniscus, from the meniscus to the middle of the mold, and from the middle of the mold to the outlet of the mold, and t...
PUM
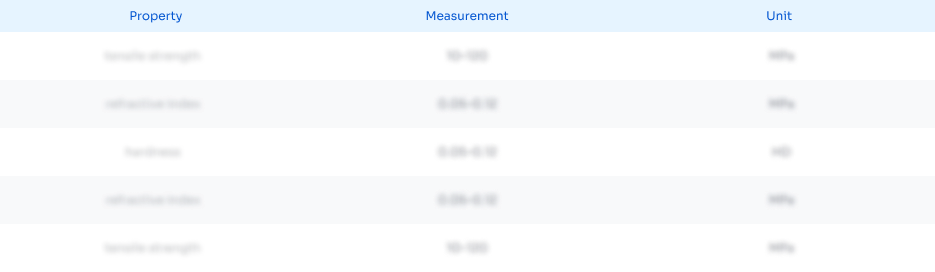
Abstract
Description
Claims
Application Information

- R&D
- Intellectual Property
- Life Sciences
- Materials
- Tech Scout
- Unparalleled Data Quality
- Higher Quality Content
- 60% Fewer Hallucinations
Browse by: Latest US Patents, China's latest patents, Technical Efficacy Thesaurus, Application Domain, Technology Topic, Popular Technical Reports.
© 2025 PatSnap. All rights reserved.Legal|Privacy policy|Modern Slavery Act Transparency Statement|Sitemap|About US| Contact US: help@patsnap.com