Pickling method of surface of 430 stainless steel
A stainless steel and pickling technology, applied in the pickling field of 430 stainless steel surface, can solve the problems of environmental pollution, increased production cost, low surface finish, etc., to avoid NOx gas and nitrite solution, save pickling cost, reduce Effect of Polishing Time
- Summary
- Abstract
- Description
- Claims
- Application Information
AI Technical Summary
Problems solved by technology
Method used
Examples
Embodiment 1
[0012] Put the annealed 430 stainless steel directly into the pickling tank for pickling. The pickling solution in the pickling tank is composed of hydrochloric acid and hydrogen peroxide with a concentration of 7mol / L. The addition of hydrogen peroxide is 0.1% of the molar number of hydrochloric acid. The pickling temperature is 50°C, the pickling residence time is 300 seconds; wash the 430 stainless steel after pickling once, the washing temperature is 20°C, and the residence time is 80 seconds; The temperature was 60°C and the residence time was 120 seconds. The surface of the stainless steel after pickling has a high degree of smoothness, which can directly replace the flat and polished treatment of the BA plate.
Embodiment 2
[0014] Put the annealed 430 stainless steel directly into the pickling tank for pickling. The pickling solution in the pickling tank is composed of 1mol / L hydrochloric acid and hydrogen peroxide. The addition of hydrogen peroxide is 3% of the mole number of hydrochloric acid. The pickling temperature is 80°C, the pickling residence time is 400 seconds; wash the 430 stainless steel after pickling once, the washing temperature is 60°C, and the residence time is 120 seconds; The temperature was 20°C and the residence time was 100 seconds. The surface of the stainless steel after pickling has a high degree of smoothness, which can directly replace the flat and polished treatment of the BA plate.
Embodiment 3
[0016] Put the 430 stainless steel after annealing directly into the pickling tank for pickling. The pickling solution in the pickling tank is composed of 5mol / L hydrochloric acid and potassium chlorate. The addition of potassium chlorate is 0.1% of the mole number of hydrochloric acid. 20°C, the pickling residence time is 500 seconds; wash the 430 stainless steel after pickling once, the washing temperature is 40°C, and the residence time is 100 seconds; The temperature was 40°C and the residence time was 80 seconds. The surface of the stainless steel after pickling has a high degree of smoothness, which can directly replace the flat and polished treatment of the BA plate.
PUM
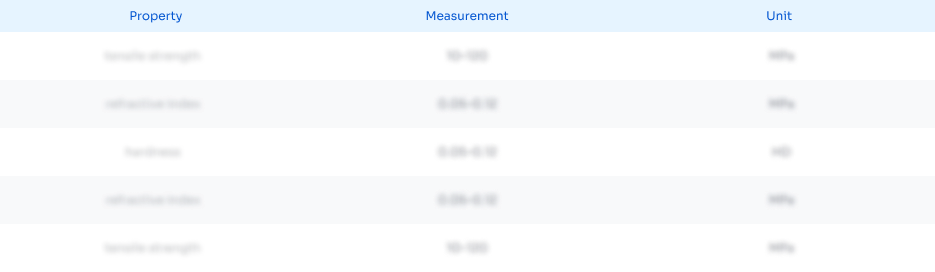
Abstract
Description
Claims
Application Information

- R&D Engineer
- R&D Manager
- IP Professional
- Industry Leading Data Capabilities
- Powerful AI technology
- Patent DNA Extraction
Browse by: Latest US Patents, China's latest patents, Technical Efficacy Thesaurus, Application Domain, Technology Topic, Popular Technical Reports.
© 2024 PatSnap. All rights reserved.Legal|Privacy policy|Modern Slavery Act Transparency Statement|Sitemap|About US| Contact US: help@patsnap.com