Local UV printing process for surface of metal printing ink
A metal ink, partial technology, applied in the field of partial UV printing process, can solve the problems of poor adhesion between UV varnish and metal ink layer, the primer does not have the function of top oil, and does not have a matte effect, etc., to protect the printing surface, Good bonding effect
- Summary
- Abstract
- Description
- Claims
- Application Information
AI Technical Summary
Problems solved by technology
Method used
Examples
Embodiment 1
[0020] A partial UV printing process on the surface of metallic ink, the process comprises the following steps:
[0021] (1) Add 12wt% styrene-acrylic acid polymer, 0.5wt% modified silica-polyethylene wax copolymer and 8wt% self-crosslinking emulsion to the UV base oil, and react at minus 20°C to obtain improved Sexual UV primer with a matte finish;
[0022] (2) After brushing a layer of metal ink on the material to be printed, apply the above-mentioned modified UV base oil, dry it by infrared radiation, and then perform partial UV varnish coating by screen printing, and then apply it with UV light. The product is obtained after irradiation and drying, and the product can optionally present glossy luster and matte luster.
[0023] The above-mentioned modified silicon dioxide-polyethylene wax copolymer is made of polyethylene (PE) ultrafine powder wax, reacted at a temperature of 80°C and a pressure of 3P, and emulsified for 6 hours, while adding a modified silicon dioxide liq...
Embodiment 2
[0025] A partial UV printing process on the surface of metallic ink, the process comprises the following steps:
[0026] (1) Add 10wt% styrene-acrylic acid polymer, 0.8wt% modified silica-polyethylene wax copolymer and 10wt% self-crosslinking emulsion to the UV base oil, and react at minus 10°C to obtain improved Sexual UV primer with a matte finish;
[0027] (2) After brushing a layer of metal ink on the material to be printed, apply the above-mentioned modified UV base oil, dry it by infrared radiation, and then perform partial UV varnish coating by screen printing, and then apply it with UV light. The product is obtained after irradiation and drying, and the product can optionally present glossy luster and matte luster.
[0028] The above-mentioned modified silicon dioxide-polyethylene wax copolymer is made of polyethylene (PE) ultrafine powder wax, reacted at a temperature of 90°C and a pressure of 3P, and emulsified for 5 hours, while adding a modified silicon dioxide li...
Embodiment 3
[0030] A partial UV printing process on the surface of metallic ink, the process comprises the following steps:
[0031] (1) Add 15wt% styrene-acrylic acid polymer, 0.2wt% modified silica-polyethylene wax copolymer and 6wt% self-crosslinking emulsion to the UV base oil, and react at minus 30°C to obtain improved Sexual UV primer with a matte finish;
[0032] (2) After brushing a layer of metal ink on the material to be printed, apply the above-mentioned modified UV base oil, dry it by infrared radiation, and then perform partial UV varnish coating by screen printing, and then apply it with UV light. The product is obtained after irradiation and drying, and the product can optionally present glossy luster and matte luster.
[0033] The above-mentioned modified silicon dioxide-polyethylene wax copolymer is made of polyethylene (PE) ultrafine powder wax, reacted at a temperature of 85°C and a pressure of 3P, and emulsified for 5.5 hours, while adding a modified silicon dioxide l...
PUM
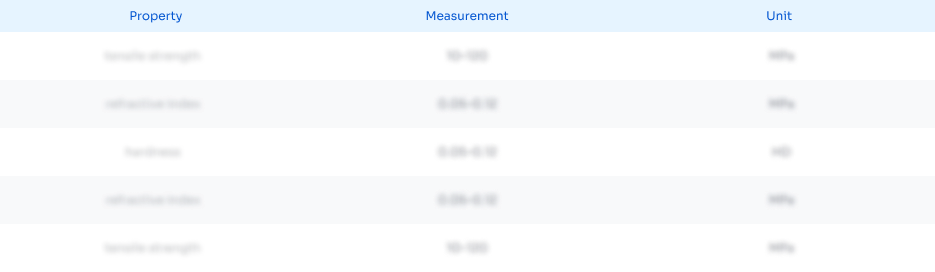
Abstract
Description
Claims
Application Information

- Generate Ideas
- Intellectual Property
- Life Sciences
- Materials
- Tech Scout
- Unparalleled Data Quality
- Higher Quality Content
- 60% Fewer Hallucinations
Browse by: Latest US Patents, China's latest patents, Technical Efficacy Thesaurus, Application Domain, Technology Topic, Popular Technical Reports.
© 2025 PatSnap. All rights reserved.Legal|Privacy policy|Modern Slavery Act Transparency Statement|Sitemap|About US| Contact US: help@patsnap.com