Special welding electrode for surfacing and repairing broken teeth of cast iron gear
A gear and tooth breaking technology, which is applied in the field of material science and engineering, can solve problems such as large cracking tendency of surfacing welding metal and heat-affected zone, tissue whitening, and increased labor intensity of workers
- Summary
- Abstract
- Description
- Claims
- Application Information
AI Technical Summary
Problems solved by technology
Method used
Examples
Embodiment Construction
[0013] The following disclosure is an example of the present invention, requiring: marble 37.4, clay 3.5, fluorite 22.7, quartz 1.7, rutile 3.8, titanium iron 5.8, molybdenum iron 2.6, high carbon ferromanganese 2.5, silicon iron 1.6, yttrium oxide 5.3, Nickel Metal 13.1. The welding core adopts H08A steel welding wire. The modulus of the binder water glass used is 2.7-3.0, and the concentration (Baume degree) is 48-50. For ferrosilicon and high-carbon ferromanganese powder, passivation treatment is required before use. The passivation process for ferrosilicon powder is 730°C, and for high-carbon ferromanganese powder is 320°C. The above metal powders are all kept warm for 1 hour. Mix the relevant powders in the above formula with a mixer, then add water glass and stir evenly, extrude the welding rod with a welding rod coating machine, dry the welding rod at 250-300°C, and then grind the head and tail.
[0014] Use the surfacing electrode manufactured above to repair the bro...
PUM
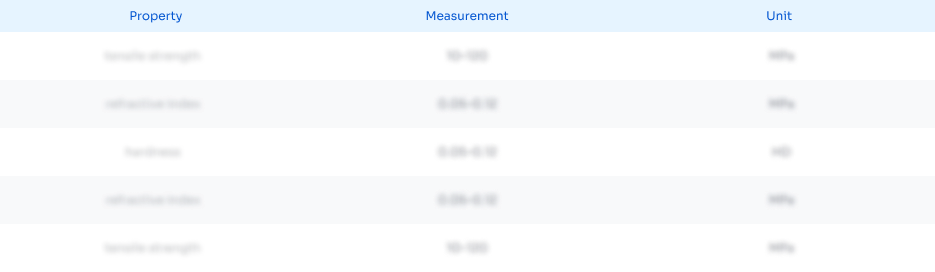
Abstract
Description
Claims
Application Information

- Generate Ideas
- Intellectual Property
- Life Sciences
- Materials
- Tech Scout
- Unparalleled Data Quality
- Higher Quality Content
- 60% Fewer Hallucinations
Browse by: Latest US Patents, China's latest patents, Technical Efficacy Thesaurus, Application Domain, Technology Topic, Popular Technical Reports.
© 2025 PatSnap. All rights reserved.Legal|Privacy policy|Modern Slavery Act Transparency Statement|Sitemap|About US| Contact US: help@patsnap.com