Method for manufacturing amorphous alloy stator iron core of high-frequency motor
A technology of amorphous alloy and stator core, which is applied in the field of preparation of amorphous alloy stator core, can solve the problems of increasing current, etc., achieve the effects of reducing eddy current loss, good product consistency and stability, and conducive to mass production
- Summary
- Abstract
- Description
- Claims
- Application Information
AI Technical Summary
Problems solved by technology
Method used
Image
Examples
Embodiment Construction
[0010] In the present invention, the conventional amorphous alloy powder is used as the raw material, and the amorphous alloy powder and the binder are fully and uniformly mixed; then the amorphous alloy powder mixed with the binder is placed in a mold and press-molded to form the desired shape and size the stator core. Amorphous alloy powder and binder are mixed at a ratio of 100:5 to 100:20; the binder is epoxy resin, varnish, acrylic resin, cyanoacrylate and other insulating materials; during the process of mixing amorphous alloy powder and binder The temperature is 120°C to 180°C; the pressure during the press molding process is 70MPA to 90MPA; the dwell time during the press molding process is 5 minutes to 10 minutes.
[0011] Such as figure 1 As shown, the embodiments of the present invention are as follows. Since the production of amorphous alloy powder has a set of mature technology, the raw materials of amorphous alloy powder of required shape and size can be directl...
PUM
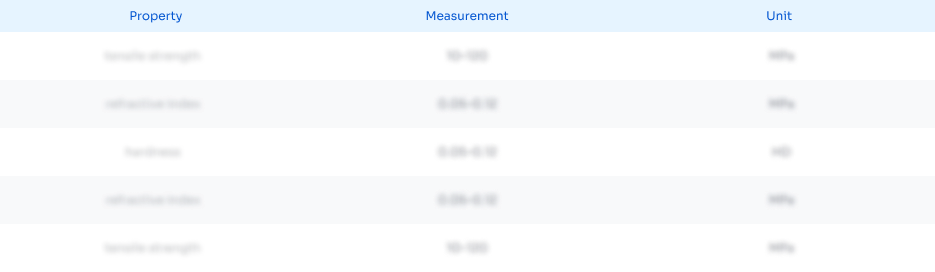
Abstract
Description
Claims
Application Information

- R&D
- Intellectual Property
- Life Sciences
- Materials
- Tech Scout
- Unparalleled Data Quality
- Higher Quality Content
- 60% Fewer Hallucinations
Browse by: Latest US Patents, China's latest patents, Technical Efficacy Thesaurus, Application Domain, Technology Topic, Popular Technical Reports.
© 2025 PatSnap. All rights reserved.Legal|Privacy policy|Modern Slavery Act Transparency Statement|Sitemap|About US| Contact US: help@patsnap.com