Heat exchanger of tobacco flue-curing house
A heat exchanger and flue-cured tobacco room technology, applied in the field of flue-cured tobacco room heat exchangers, can solve the problems of uneven output temperature, low output heat, and high exhaust temperature
- Summary
- Abstract
- Description
- Claims
- Application Information
AI Technical Summary
Problems solved by technology
Method used
Image
Examples
Embodiment 1
[0016] Such as figure 1 A kind of heat exchanger of flue-cured tobacco room shown, it comprises furnace heat flue gas inlet 1, front gas collecting box, heat exchange tube, rear gas collecting box 7, smoke exhaust chimney 4, the two ends of heat exchanging tube are connected with front collecting box respectively The gas box is connected with the rear gas collection box 7 and forms a passage for smoke gas in and out. A horizontal front gas collection box partition 12 is designed in the middle of the front gas collection box, and the front gas collection box partition 12 divides the front gas collection box into front gas collection boxes. The upper chamber 10 of the tank and the lower chamber 3 of the front gas collection box, the heat exchange tube connected with the lower chamber 3 of the front gas collection box is a return heat exchange pipe 8, and the heat exchange pipe connected with the upper chamber 10 of the front gas collection box is a second return heat exchange pip...
PUM
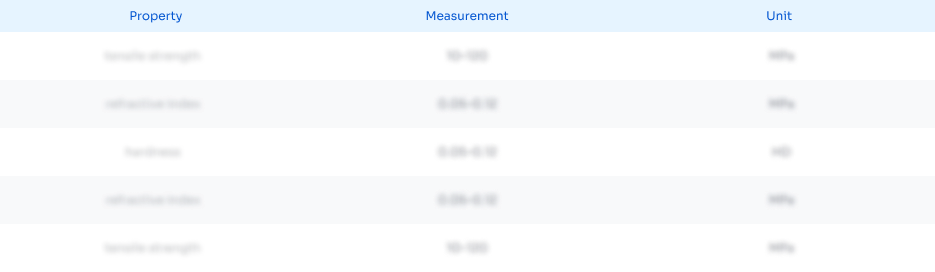
Abstract
Description
Claims
Application Information

- R&D
- Intellectual Property
- Life Sciences
- Materials
- Tech Scout
- Unparalleled Data Quality
- Higher Quality Content
- 60% Fewer Hallucinations
Browse by: Latest US Patents, China's latest patents, Technical Efficacy Thesaurus, Application Domain, Technology Topic, Popular Technical Reports.
© 2025 PatSnap. All rights reserved.Legal|Privacy policy|Modern Slavery Act Transparency Statement|Sitemap|About US| Contact US: help@patsnap.com