Method for manufacturing printed wiring board
A technology for printed wiring boards and wiring patterns, which is applied in the manufacture of printed circuit precursors, printed circuits, printed circuit manufacturing, etc. It can solve the problems of difficult positioning and positioning in the photolithography process, and achieve the effect of high productivity
- Summary
- Abstract
- Description
- Claims
- Application Information
AI Technical Summary
Problems solved by technology
Method used
Image
Examples
Embodiment 1
[0088] In this example, Figure 1A and 1B An example of a method of forming a circuit by a semi-additive method using a polyimide film on both sides of which a copper foil sheet with a carrier is laminated is exemplified in .
[0089] Such as Figure 1A As shown in (a), there is provided a polyimide film 101 on both sides of which a copper foil sheet with a carrier is laminated. This double-sided copper foil laminated polyimide film 101 with a carrier includes a copper foil 3 with a carrier, a polyimide film 2 and a copper foil 3' with a carrier laminated in this order, each of which has a carrier The copper foils (3, 3') are laminated layers of respective copper foils (4, 4') and carrier foils (5, 5') as protective layers. Here, the thickness of the copper foil is in the range of 1 to 8 μm, preferably in the range of 1 to 6 μm.
[0090] In the next step, as Figure 1A Shown in (b), utilize the copper foil 3 that has carrier, polyimide film 2 and copper foil 4 ' on one si...
Embodiment 2
[0106] In this example, Figure 2A and 2B exemplifies a process example of forming a circuit by a semi-additive method using a polyimide film laminated with a copper foil sheet with a carrier on both sides.
[0107] Such as Figure 2A As shown in (a), there is provided a polyimide film 101 laminated with copper foil with a carrier on both sides. In this double-sided copper foil laminated polyimide film with carrier 101, copper foil 3 with carrier, polyimide film 2, and copper foil 3' with carrier are laminated in this order, with carrier The copper foils (3, 3') are laminates of copper foils (4, 4') and carrier foils (5, 5'), where the thickness of the copper foils ranges from 1 to 8 μm, preferably from 1 to 8 μm. 6 μm.
[0108] In the next step, as Figure 2A As shown in (b), a through hole is formed at a predetermined position of the double-sided copper foil laminated polyimide film 101 with a carrier through the copper foil 3 with a carrier and the polyimide film 2 on ...
Embodiment 3
[0118] In this example, image 3 An example of a method of forming a via hole in the via hole forming process of Embodiments 1 and 2 is illustrated.
[0119] Such as image 3 As shown in (a), there is provided a polyimide film 101 on both sides of which a copper foil sheet with a carrier is laminated. This double-sided copper foil laminated polyimide film 101 with a carrier includes a copper foil 3 with a carrier, a polyimide film 2 and a copper foil 3' with a carrier, each of which has a copper foil with a carrier Foils (3, 3') are laminates of respective copper foils (4, 4') and carrier foils (5, 5') as protective layers, the copper foils having a thickness in the range of 1 to 8 μm, preferably in the range of 1 to 6 μm.
[0120] In the next step, as image 3 As shown in (b), utilize laser etc. to pass through copper foil 3 and 3 ' both sides with carrier and polyimide film 2, form on a part of double-sided copper foil laminated polyimide film 101 with carrier Through h...
PUM
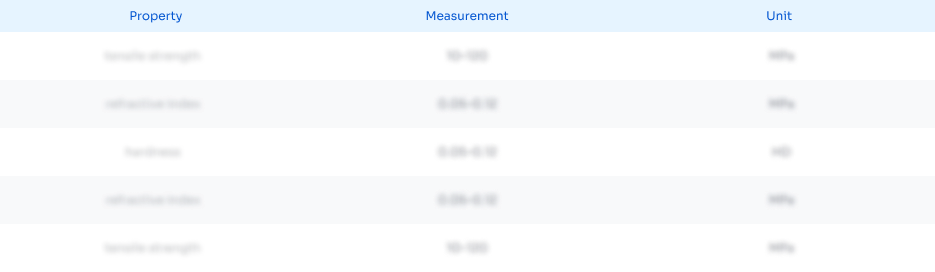
Abstract
Description
Claims
Application Information

- R&D
- Intellectual Property
- Life Sciences
- Materials
- Tech Scout
- Unparalleled Data Quality
- Higher Quality Content
- 60% Fewer Hallucinations
Browse by: Latest US Patents, China's latest patents, Technical Efficacy Thesaurus, Application Domain, Technology Topic, Popular Technical Reports.
© 2025 PatSnap. All rights reserved.Legal|Privacy policy|Modern Slavery Act Transparency Statement|Sitemap|About US| Contact US: help@patsnap.com