Process for processing smoke
A flue gas treatment and process technology, applied in the field of metallurgy, can solve the problems of poor flue gas treatment effect, low zinc recovery rate, and large zinc recovery flue gas treatment capacity, so as to reduce equipment investment and operating costs, and reduce the scale of equipment and equipment. Small, save the effect of investment and operation cost
- Summary
- Abstract
- Description
- Claims
- Application Information
AI Technical Summary
Problems solved by technology
Method used
Image
Examples
Embodiment 1
[0020] Embodiment 1, a kind of flue gas treatment process, this process carries out the staged treatment of the flue gas produced by the rotary hearth furnace;
[0021] The atmosphere in the oxidation heating zone is oxidative, the oxygen content in the flue gas is controlled at 2%, and the temperature is 800°C to 900°C. The flue gas volume in this area accounts for 35% of the total flue gas volume, and the gasification emission of zinc accounts for the total 2% of zinc gasification emissions. The main function of this area is to heat the green pellets to increase the temperature;
[0022] The flue gas in the oxidation heating zone is sent to the green pellet drying chamber in front of the rotary hearth furnace process to dry and preheat the green pellets;
[0023] The flue gas in the high-temperature reduction zone is reductive. The flue gas mainly contains incompletely combusted CO. The temperature of the flue gas is between 950°C and 1350°C. The gas volume accounts for 65...
PUM
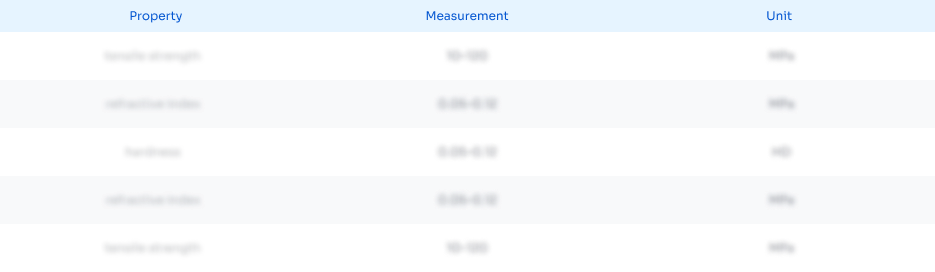
Abstract
Description
Claims
Application Information

- R&D
- Intellectual Property
- Life Sciences
- Materials
- Tech Scout
- Unparalleled Data Quality
- Higher Quality Content
- 60% Fewer Hallucinations
Browse by: Latest US Patents, China's latest patents, Technical Efficacy Thesaurus, Application Domain, Technology Topic, Popular Technical Reports.
© 2025 PatSnap. All rights reserved.Legal|Privacy policy|Modern Slavery Act Transparency Statement|Sitemap|About US| Contact US: help@patsnap.com