Method for preparing nanocomposite hybrid multi-dimension material
A composite material and nanocomposite technology, applied in the field of preparation of hybrid multi-scale composite materials, can solve the problems of single structure and function, low heat resistance, etc., and achieve the effect of broad application prospects
- Summary
- Abstract
- Description
- Claims
- Application Information
AI Technical Summary
Problems solved by technology
Method used
Image
Examples
Embodiment 1
[0020] (1) Disperse the carbon nanotubes in the epoxy resin, ultrasonically disperse for 1h, the ultrasonic power is 100W, the ultrasonic frequency is 20kHz, and the amount of carbon nanotubes is 1% of the resin amount;
[0021] (2) Fill the nano-composite resin matrix into the mold with the upper wall plate made of ceramics under the combined action of vacuum and 0.2MPa external pressure. The interior of the mold has been pre-filled with carbon fiber fabric reinforcements. The filling process is carried out in an ultrasonic field. The power of the ultrasound is 260W and the frequency is 40kHz.
[0022] (3) Put the filled mold into an oven for curing, and obtain a hybrid multi-scale composite material after demoulding.
Embodiment 2
[0024] The differences between this embodiment and Embodiment 1 are: the dosage of carbon nanotubes is 0.5% of the resin dosage, the ultrasonic dispersion is 2 hours, the power is 80W, and the ultrasonic frequency is 30kHz.
Embodiment 3
[0026] The difference between this example and Example 1 is that the resin used is unsaturated polyester, the ultrasonic dispersion is 2 hours, the power is 40W, and the ultrasonic frequency is 45kHz.
PUM
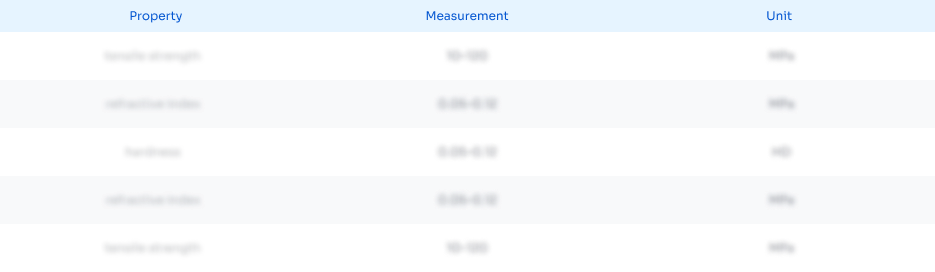
Abstract
Description
Claims
Application Information

- R&D
- Intellectual Property
- Life Sciences
- Materials
- Tech Scout
- Unparalleled Data Quality
- Higher Quality Content
- 60% Fewer Hallucinations
Browse by: Latest US Patents, China's latest patents, Technical Efficacy Thesaurus, Application Domain, Technology Topic, Popular Technical Reports.
© 2025 PatSnap. All rights reserved.Legal|Privacy policy|Modern Slavery Act Transparency Statement|Sitemap|About US| Contact US: help@patsnap.com