Synthesis method of waterborne polyurethane emulsion
A technology of water-based polyurethane and synthesis method, applied in the field of synthesis of water-based polyurethane emulsion, can solve the problems of unstable product state, large differences in the degree of difficulty of water dispersion, loss of water-dispersibility of synthetic products, etc., and achieve the effect of avoiding side reactions
- Summary
- Abstract
- Description
- Claims
- Application Information
AI Technical Summary
Problems solved by technology
Method used
Image
Examples
Embodiment 1
[0030] Embodiment 1 (acetone method)
[0031] Weigh 125.6g of polyether polyol MN-3050 into a 1000ml three-necked flask, and vacuum dehydrate it in an oil bath at 110-120°C for 1 hour. Then cool down to 70°C, add 15g isophorone diisocyanate (IPDI), 17.7g dicyclohexylmethane diisocyanate (HMDI), 6.3g dimethylolpropionic acid (DMPA), 2d dibutyltin dilaurate as a catalyst , and 10ml of acetone was added as a diluent, the temperature was raised and the oil bath was controlled at 80-90°C, and the reaction was stirred for 2h. Lower the temperature and control the oil bath to 70-80°C, then add 2.3g of butanediol and 6ml of acetone, react for 1 hour and then cool down to 40°C, add 9.5g of triethylamine-dichloromethane complex, stir well, then add 200ml of water, Stirring was continued for 1 h to obtain a white emulsion with a solid content of 45%.
Embodiment 2
[0032] Embodiment 2 (acetone method)
[0033] Weigh 100g polybutylene adipate (M n =1000) in a 1000ml three-neck flask, vacuum dehydrated in an oil bath at 110-120°C for 1h. Then cool down to 80°C, add 76g isophorone diisocyanate (IPDI), 7.0g dimethylolpropionic acid (DMPA), 2d dibutyltin dilaurate as catalyst, and add 10ml acetone as diluent, control the oil bath 80 ~ 90 ° C, stirred for 2 hours. Then add 4.1g of diethylene glycol and 20ml of acetone, react for 2h, then cool down to 40°C, add 10.0g of triethylamine-dichloromethane complex for neutralization reaction, then add 190ml of water, stir and disperse to obtain solid 50% white emulsion.
Embodiment 3
[0034] Embodiment 3 (prepolymer method)
[0035]Weigh 50g of polyether polyol MN-3050 into a 500ml three-neck flask, and vacuum dehydrate it in an oil bath at 110-120°C for 1 hour. Then cool down to 70°C, add 13.3g of isophorone diisocyanate (IPDI), 8.4g of hexamethylene diisocyanate (HDI), 1d of dibutyltin dilaurate as a catalyst, heat up and control the oil bath at 80-90°C, The reaction was stirred for 2h. Add 6.3g of dimethylolpropionic acid (DMPA) and 8ml of acetone, control the oil bath at 70-80°C, and stir for 1h. Then the temperature was lowered to 40° C., and 9.5 g of triethylamine-dichloromethane complex was added for neutralization to obtain a prepolymer. Slowly add this prepolymer into 130ml of aqueous solution in which 3.0g of ethylenediamine is dissolved under the condition of rapid stirring, and obtain a white emulsion with a solid content of 40% after dispersion.
PUM
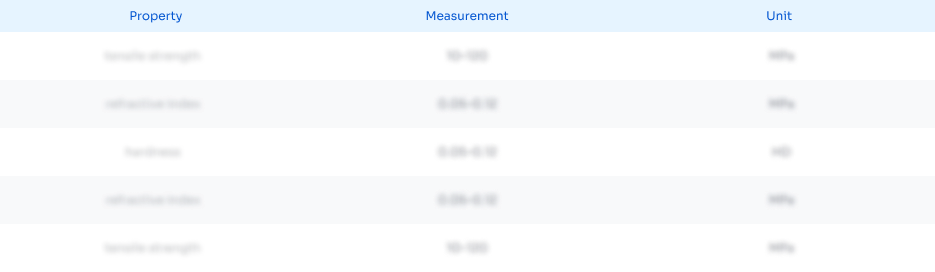
Abstract
Description
Claims
Application Information

- R&D
- Intellectual Property
- Life Sciences
- Materials
- Tech Scout
- Unparalleled Data Quality
- Higher Quality Content
- 60% Fewer Hallucinations
Browse by: Latest US Patents, China's latest patents, Technical Efficacy Thesaurus, Application Domain, Technology Topic, Popular Technical Reports.
© 2025 PatSnap. All rights reserved.Legal|Privacy policy|Modern Slavery Act Transparency Statement|Sitemap|About US| Contact US: help@patsnap.com