Method for hydrogenation and catalytic cracking of residual oil
A catalytic cracking and hydrotreating technology, applied in the production of gasoline products, can solve the problems of increased investment costs, limited naphtha and diesel yield, and reduced total yield, so as to reduce equipment investment and operating energy consumption, save Duplicate processing steps, reduce the effect of heat exchange equipment
- Summary
- Abstract
- Description
- Claims
- Application Information
AI Technical Summary
Problems solved by technology
Method used
Image
Examples
Embodiment
[0032] This embodiment adopts the combined method of residual oil hydrotreating and catalytic cracking provided by the present invention, and all the liquid phase products of hydrotreating directly enter the catalytic cracking unit without fractionation, and the fractionation system of catalytic cracking reaction effluent is simplified in design, and only the dry gas is fractionated out , liquefied petroleum gas and gasoline fractions, catalytic cracking diesel oil, catalytic cracking cycle oil and catalytic oil slurry are directly used as catalytic cracking heavy fractions without fractionation. The catalytic cracking heavy fractions are filtered out of solid impurities and then recycled to the hydrotreating unit for further processing. Table 2, Table 3, and Table 5 are process conditions, product distribution, and main product properties, respectively.
[0033] The comparison results show that after hydrotreating the FCC heavy distillate oil and the fresh residue raw material...
PUM
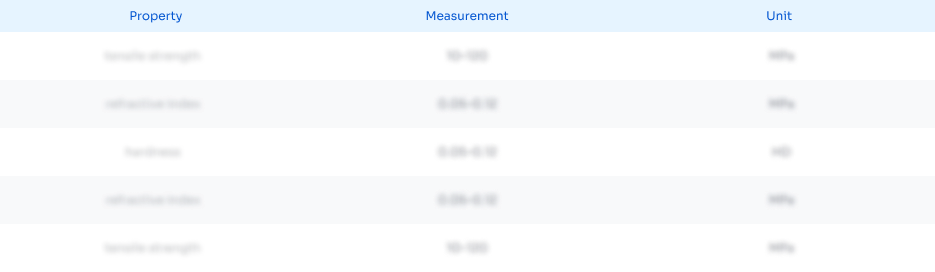
Abstract
Description
Claims
Application Information

- R&D
- Intellectual Property
- Life Sciences
- Materials
- Tech Scout
- Unparalleled Data Quality
- Higher Quality Content
- 60% Fewer Hallucinations
Browse by: Latest US Patents, China's latest patents, Technical Efficacy Thesaurus, Application Domain, Technology Topic, Popular Technical Reports.
© 2025 PatSnap. All rights reserved.Legal|Privacy policy|Modern Slavery Act Transparency Statement|Sitemap|About US| Contact US: help@patsnap.com