Process for preparing moulded zeolite by utilizing coal ash
A technology for fly ash and zeolite, which is applied in inorganic chemistry, chemical instruments and methods, molecular sieves and alkali exchange compounds, etc., can solve the problems of adsorbent or catalyst carrier limitation, limitation of industrial application scope, decrease in adsorption performance, etc. Pre-activation process, solving limitations and high costs, improving plasticity
- Summary
- Abstract
- Description
- Claims
- Application Information
AI Technical Summary
Problems solved by technology
Method used
Image
Examples
Embodiment 1
[0044] Mix 30g of fly ash, 35g of Al(OH), 5g of NaOH, 3g of sodium carboxymethylcellulose and 18mL of water, seal it and put it in a steam bath at 60°C for 5 hours; Extrude and granulate on a kneading extruder; then put the granular material in a crystallization kettle with water, seal it and put it in an oven at 200°C for 12 hours; after curing, cool the crystallization kettle to room temperature with tap water; then take it out The material is placed in a temperature-programmed furnace, raised from room temperature to 700°C and kept for 6 hours, and the heating and cooling rate is controlled at 2°C / min; finally, the material is placed in a 5.0mol / L NaOH solution for zeolization, and the NaOH solution The liquid-solid ratio to the material is 15ml / g, the zeolization temperature is 120°C, and the time is 48h. Wash until neutral and dry to obtain granular zeolite.
Embodiment 2
[0046] Similar to the preparation method of the granular zeolite in Example 1, the difference lies in the ratio of raw materials, the concentration of NaOH solution and the zeolization temperature. Among them, the amount of fly ash, Al (OH) 3, NaOH, sodium carboxymethyl cellulose and water is 60g, 25g, 15g, 10g and 50mL respectively; the zeolization temperature is 100°C; the concentration of NaOH solution is 3mol / L.
Embodiment 3
[0048]Similar to the preparation method of granular zeolite in Example 1, the difference is that the amounts of fly ash, Al(OH) 3, NaOH, sodium carboxymethylcellulose and water are 45g, 15g, 10g, 6g and 30mL.
PUM
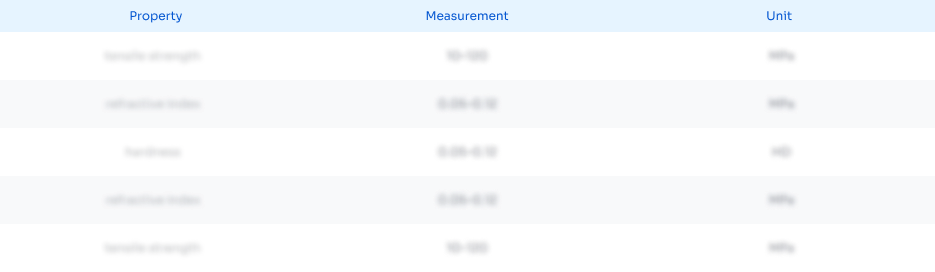
Abstract
Description
Claims
Application Information

- R&D
- Intellectual Property
- Life Sciences
- Materials
- Tech Scout
- Unparalleled Data Quality
- Higher Quality Content
- 60% Fewer Hallucinations
Browse by: Latest US Patents, China's latest patents, Technical Efficacy Thesaurus, Application Domain, Technology Topic, Popular Technical Reports.
© 2025 PatSnap. All rights reserved.Legal|Privacy policy|Modern Slavery Act Transparency Statement|Sitemap|About US| Contact US: help@patsnap.com