Ultrasonic soldering flux coating process and device
A technology for coating device and flux, which is applied to devices for coating liquid on surfaces, spray devices, liquid spray devices, etc., which can solve the problems of complicated operation, complicated internal mechanism, and the size and speed of spray volume are easily affected by flux flow rate. The size and flow rate of the impact of other issues, to achieve the effect of strong adhesion and good wettability
- Summary
- Abstract
- Description
- Claims
- Application Information
AI Technical Summary
Problems solved by technology
Method used
Image
Examples
Embodiment Construction
[0015] The present invention will be described in further detail below in conjunction with the embodiments and with reference to the accompanying drawings.
[0016] An ultrasonic flux coating process, the process steps are:
[0017] In the first step, flux is injected into the flux box 7 installed in the bottom box 9 of the ultrasonic flux coating box and the bottom is equipped with a 60KHz ultrasonic atomizer 8, and the liquid level of the flux is higher than that capable of immersing the ultrasonic mist the position of the carburetor 8;
[0018] In the second step, according to the distribution position of the solder joints on the PCBA to be welded, select a suitable nozzle board 1 and install it on the top of the top box 4 coated with ultrasonic flux, and at the same time, according to the number of solder joints on the PCBA to be soldered and the nozzle board 1 The size of the nozzle 2 adjusts the input current of the 60KHz ultrasonic atomizer 8, thereby controlling the a...
PUM
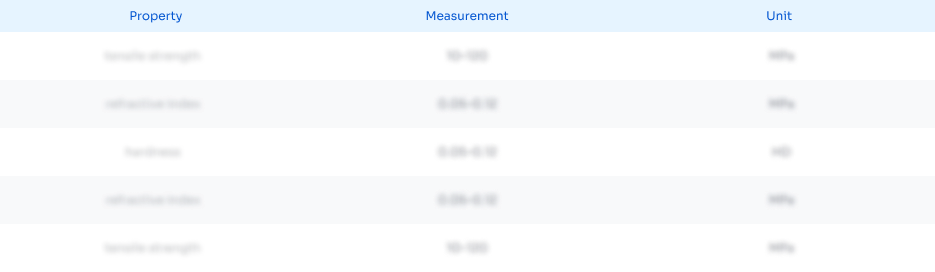
Abstract
Description
Claims
Application Information

- R&D
- Intellectual Property
- Life Sciences
- Materials
- Tech Scout
- Unparalleled Data Quality
- Higher Quality Content
- 60% Fewer Hallucinations
Browse by: Latest US Patents, China's latest patents, Technical Efficacy Thesaurus, Application Domain, Technology Topic, Popular Technical Reports.
© 2025 PatSnap. All rights reserved.Legal|Privacy policy|Modern Slavery Act Transparency Statement|Sitemap|About US| Contact US: help@patsnap.com