Selective hydrogenation catalyst for catalytic cracking gasoline and preparation method thereof
A technology of catalytic cracking gasoline and hydrogenation catalyst, which is applied in the direction of selective hydrogenation refining, catalyst activation/preparation, physical/chemical process catalyst, etc., can solve the problems of unreported demercaptan function, etc., to save equipment investment, not easy Effects of bleed, high diene hydrogenation selectivity and stability
- Summary
- Abstract
- Description
- Claims
- Application Information
AI Technical Summary
Problems solved by technology
Method used
Image
Examples
Embodiment 1
[0048] 13 g of titanium aluminum powder, 187 g of pseudo-boehmite, and 10 g of succulent powder were added, and mixed uniformly. Then kneaded and extruded into clover-shaped strips with a diameter of 2.0mm, and then roasted in a muffle furnace. The control conditions were: constant temperature at 600 °C for 2 hours and constant temperature at 800 °C for 3 hours to obtain carrier A, whose properties are shown in Table-1 . 10.18g of ammonium heptamolybdate was weighed and dissolved in 100ml of 20% ammonia water, 53.80g of nickel nitrate was added, and a clear and transparent solution was obtained after fully dissolving. Impregnate carrier A, dry it in the air, and then dry it in an electric oven. The control conditions are: constant temperature at 60°C for 2 hours and then constant temperature at 110°C for 3 hours. After drying, the material is roasted in a muffle furnace. The control conditions are: constant temperature at 350°C for 2 hours. 480 ℃ constant temperature for 2 ho...
Embodiment 2
[0050] 26g of titanium-aluminum powder, 174g of pseudo-boehmite, and 10g of asparagus powder were added, and mixed uniformly. Then kneaded and extruded into clover-shaped strips with a diameter of 2.0mm, and then roasted in a muffle furnace. The control conditions were: constant temperature at 600 °C for 2 hours and constant temperature at 800 °C for 3 hours to obtain carrier B, whose properties are shown in Table-1 . 11.65g of ammonium heptamolybdate was weighed and dissolved in 100ml of 20% ammonia water, 46.47g of nickel nitrate was added, and a clear and transparent solution was obtained after fully dissolving. The carrier B is impregnated, dried in the air, and then dried in an electric oven. The control conditions are: constant temperature at 60 °C for 2 hours and constant temperature at 110 °C for 3 hours. After drying, the material is roasted in a muffle furnace. The control conditions are: constant temperature at 350 °C for 2 hours 480 ℃ constant temperature for 2 ho...
Embodiment 3
[0052] 52g of titanium-aluminum powder, 148g of pseudo-boehmite, and 10g of asparagus powder were added, and mixed uniformly. Then kneaded and extruded into clover-shaped strips with a diameter of 2.0 mm, and then roasted in a muffle furnace. The control conditions were: constant temperature at 600 °C for 2 hours and constant temperature at 800 °C for 3 hours to obtain carrier C, whose properties are shown in Table-1 , 15.09g of ammonium heptamolybdate was weighed and dissolved in 100ml of 20% ammonia water, 40.60g of nickel nitrate was added, and a clear and transparent solution was obtained after fully dissolving. Impregnate the carrier C, dry it in the air, and then dry it in an electric oven. The control conditions are: constant temperature at 60°C for 2 hours and constant temperature at 110°C for 3 hours. After drying, the material is roasted in a muffle furnace. The control conditions are: constant temperature at 350°C for 2 hours. 480 ℃ constant temperature for 2 hours ...
PUM
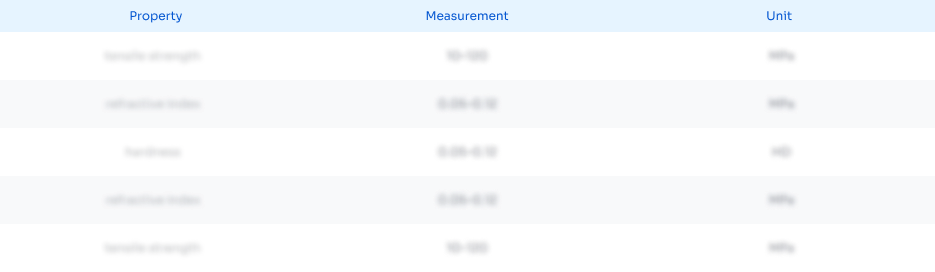
Abstract
Description
Claims
Application Information

- R&D Engineer
- R&D Manager
- IP Professional
- Industry Leading Data Capabilities
- Powerful AI technology
- Patent DNA Extraction
Browse by: Latest US Patents, China's latest patents, Technical Efficacy Thesaurus, Application Domain, Technology Topic, Popular Technical Reports.
© 2024 PatSnap. All rights reserved.Legal|Privacy policy|Modern Slavery Act Transparency Statement|Sitemap|About US| Contact US: help@patsnap.com