Cyanate resin modified by phenylacetylene base silane resin and preparation method thereof
A technology of phenylethynyl silane and cyanate ester resin, which is applied in the field of new polymer materials and their preparation
- Summary
- Abstract
- Description
- Claims
- Application Information
AI Technical Summary
Problems solved by technology
Method used
Image
Examples
Embodiment 1
[0031] First, mix 100 parts (parts by mass) of bisphenol A type cyanate resin with 10 parts of methyl toluene ethynyl silane resin in acetone, and after completely dissolving, heat and distill off the solvent to prepare methyl toluene Ethynyl silane resin modified bisphenol A type cyanate resin blend. The above blend is cured under a certain curing process. The curing process is 110°C / 1h→150°C / 1h→200°C / 2h→250°C / 2h→300°C / 4h to obtain a methyl tolanyl Silane resin modified bisphenol A cyanate resin.
Embodiment 2
[0033] First, mix 100 parts (parts by mass) of bisphenol A type cyanate resin with 80 parts of tetraphenylethynyl silane resin in acetone, and after completely dissolving, heat and distill off the solvent to prepare tetraphenylethynyl silane resin Modified bisphenol A type cyanate resin blend. The above blend is cured under a certain curing process. The curing process is 110°C / 1h→150°C / 1h→200°C / 4h→250°C / 4h→300°C / 4h to obtain a tetraphenylethynyl silane resin Modified bisphenol A cyanate resin.
Embodiment 3
[0035] First, mix 100 parts (parts by mass) of phenolic cyanate resin with 50 parts of methyltriphenylethynyl silane resin in acetone, and after completely dissolving, heat and distill off the solvent to prepare methyltriphenylethynyl silane resin. Silane resin modified phenolic cyanate resin blend. The above blend is cured under a certain curing process. The curing process is 110°C / 1h→150°C / 1h→200°C / 2h→250°C / 2h→300°C / 4h to obtain a triphenylethynyl silane resin Modified phenolic cyanate resin.
PUM
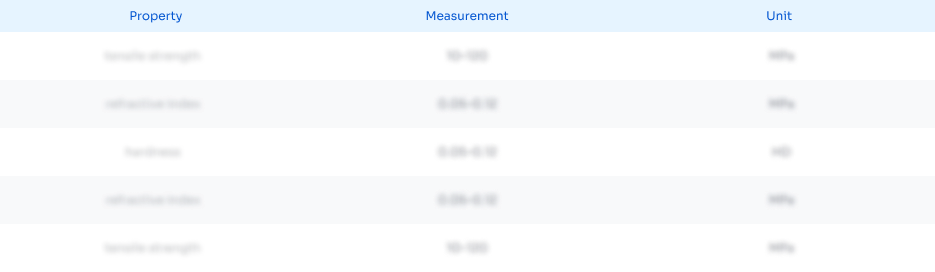
Abstract
Description
Claims
Application Information

- Generate Ideas
- Intellectual Property
- Life Sciences
- Materials
- Tech Scout
- Unparalleled Data Quality
- Higher Quality Content
- 60% Fewer Hallucinations
Browse by: Latest US Patents, China's latest patents, Technical Efficacy Thesaurus, Application Domain, Technology Topic, Popular Technical Reports.
© 2025 PatSnap. All rights reserved.Legal|Privacy policy|Modern Slavery Act Transparency Statement|Sitemap|About US| Contact US: help@patsnap.com