Catalyst for preparing isobutene through dehydrogenation of iso-butane and preparation method thereof
A technology for producing isobutene and catalysts, applied in molecular sieve catalysts, chemical instruments and methods, physical/chemical process catalysts, etc., can solve the problems of poor stability of isobutane dehydrogenation reaction, reduction of stabilization effect of platinum group metals, uneven dispersion, etc. problems, to achieve the effect of improving the catalytic activity of isobutane, excellent anti-coking performance, and high conversion rate of isobutane
- Summary
- Abstract
- Description
- Claims
- Application Information
AI Technical Summary
Problems solved by technology
Method used
Examples
Embodiment 1
[0017] Take cetyltrimethylammonium bromide and polyethylene glycol octylphenyl ether as a mixed template (the molar ratio of cetyltrimethylammonium bromide to polyethylene glycol octylphenyl ether is 3:1). Based on the molar amount of the mixed template agent, at 30° C., the molar ratio of aluminum isopropoxide to the mixed template agent is 8:1, and the molar ratio of water to the mixed template agent is 20:1. Put aluminum isopropoxide, dibutyltin oxide, water, and a mixed template into the reaction kettle, react for 15 hours, age at room temperature for 10 hours, filter, wash with absolute ethanol, dry at 120°C for 8 hours, and roast at 500°C for 6 hours to obtain A mesoporous alumina molecular sieve carrier with a tin-containing skeleton (the mass percentage of tin metal is 0.6 wt%). At 80°C, the mesoporous alumina molecular sieve carrier with a tin-containing skeleton impregnated with an auxiliary alkaline metal KCl aqueous solution for 3 hours, evaporated to dryness, dri...
Embodiment 2
[0021] Use N-dehydroabietyl-N, N, N-trimethylammonium methyl sulfate and polyoxyethylene-polyoxypropylene-polyoxyethylene as a mixed template (N-dehydroabietyl-N, N, N - The molar ratio of ammonium trimethyl sulfate methyl ester to polyoxyethylene-polyoxypropylene-polyoxyethylene two templates is 4:1). Based on the molar amount of the mixed template agent, at 40°C, the molar ratio of aluminum tri-sec-butyl alkoxide to the mixed template agent is 10:1, and the molar ratio of water to the mixed template agent is 30:1. Put aluminum tri-sec-butyl alkoxide, dibutyltin dimethoxide, water, and a mixed template into the reaction kettle, react for 25 hours, age at room temperature for 8 hours, filter, wash with absolute ethanol, and dry at 150°C for 8 hours, 500 Calcined at ℃ for 8 hours to obtain a mesoporous alumina molecular sieve carrier with a tin-containing framework (the mass percentage of tin metal is 1.2 wt%). At 80°C, impregnate the mesoporous alumina molecular sieve carrier...
Embodiment 3
[0024] Using N-dehydroabietyl-N, N-dimethyl-N-benzyl ammonium chloride and octadecyl primary amine as a mixed template (N-dehydroabietyl-N, N-dimethyl- The molar ratio of N-benzyl ammonium chloride to octadecyl primary amine is 3:1). Based on the molar amount of the mixed template agent, at 40° C., the molar ratio of aluminum isopropoxide to the mixed template agent is 8:1, and the molar ratio of water to the mixed template agent is 25:1. Put aluminum isopropoxide, distannoxane, water, and mixed template into the reaction kettle, react for 30 hours, age at room temperature for 10 hours, filter, wash with absolute ethanol, dry at 150°C for 10 hours, and roast at 600°C for 10 hours to obtain the skeleton A tin-containing mesoporous alumina molecular sieve carrier (the mass percentage of tin metal is 1.5 wt%). At 80°C, impregnate the mesoporous alumina molecular sieve carrier with a tin-containing skeleton as an alkaline metal La(NO 3 ) 3 The aqueous solution was evaporated to...
PUM
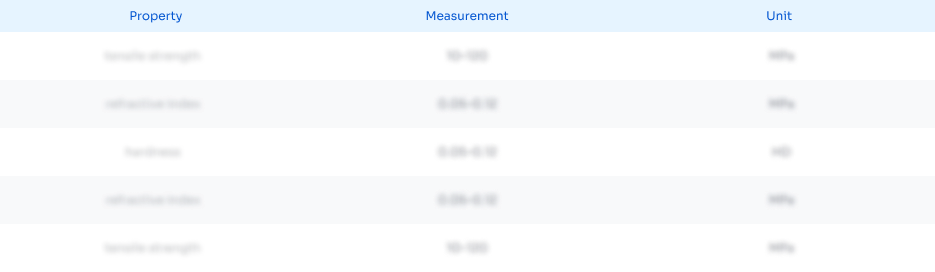
Abstract
Description
Claims
Application Information

- Generate Ideas
- Intellectual Property
- Life Sciences
- Materials
- Tech Scout
- Unparalleled Data Quality
- Higher Quality Content
- 60% Fewer Hallucinations
Browse by: Latest US Patents, China's latest patents, Technical Efficacy Thesaurus, Application Domain, Technology Topic, Popular Technical Reports.
© 2025 PatSnap. All rights reserved.Legal|Privacy policy|Modern Slavery Act Transparency Statement|Sitemap|About US| Contact US: help@patsnap.com