Sputtering apparatus and film forming method
A technology of sputtering device and film forming method, which is applied in sputtering coating, vacuum evaporation coating, coating, etc., which can solve the problems of increased film thickness, difficulty in obtaining a uniform film, and inability to form a film. , to achieve the effect of high uniformity of film thickness
- Summary
- Abstract
- Description
- Claims
- Application Information
AI Technical Summary
Problems solved by technology
Method used
Image
Examples
Embodiment Construction
[0041] figure 1 The structure of the sputtering apparatus 2 which implements this invention is shown. The vacuum chamber 3 is, for example, substantially cylindrical in shape made of stainless steel. A cylindrical turntable 4 is disposed inside the vacuum chamber 3 . The turntable 4 is rotatable around a rotating shaft 4a perpendicular to the vacuum chamber 3, and is rotated at a predetermined speed by a motor (not shown).
[0042] A vacuum pump 5 is connected to the vacuum tank 3, and the inside of the vacuum layer 3 is adjusted to a vacuum degree required for sputtering during film formation. In addition, the turntable 4 may be rotated about a horizontal rotation axis. In addition, in order to carry out operations such as loading and unloading of the workpiece W, target replacement, inspection and refurbishment described later, the vacuum chamber 3 is opened by a known structure after leaking to atmospheric pressure.
[0043] On the outer peripheral surface of the turnta...
PUM
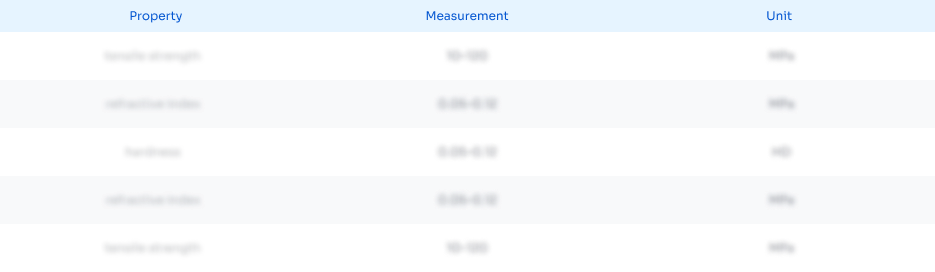
Abstract
Description
Claims
Application Information

- R&D
- Intellectual Property
- Life Sciences
- Materials
- Tech Scout
- Unparalleled Data Quality
- Higher Quality Content
- 60% Fewer Hallucinations
Browse by: Latest US Patents, China's latest patents, Technical Efficacy Thesaurus, Application Domain, Technology Topic, Popular Technical Reports.
© 2025 PatSnap. All rights reserved.Legal|Privacy policy|Modern Slavery Act Transparency Statement|Sitemap|About US| Contact US: help@patsnap.com