Method for producing white matte by mixed smelting of scrap copper and copper concentrate
A technology for scrap copper and copper concentrate, applied in the direction of improving process efficiency, can solve the problems of high copper content in slag, small amount of scrap copper, frequent operation, etc., so as to improve the utilization rate of sulfur and save facility investment. , The effect of process energy saving and environmental protection
- Summary
- Abstract
- Description
- Claims
- Application Information
AI Technical Summary
Problems solved by technology
Method used
Examples
Embodiment 1
[0020] The composition of the copper concentrate used is:
[0021] the element
Cu(%)
Fe(%)
S(%)
SiO 2 (%)
As(%)
MgO+Al 2 o 3 (%)
content
26
28
28
14
0.4
2.5
[0022] The composition of anthracite used as fuel is:
[0023] Element
Volatile matter
Ash
total
%
70.00
10.00
20.00
100.00
[0024] The batching is carried out according to the mass ratio of the copper content of the copper concentrate to the copper content of the waste miscellaneous copper = 1:0.5. In the smelting operation process of the top-blown furnace (inner diameter 4 meters, furnace height 17.6 meters), add 30 tons of copper concentrate and scrap copper scraps with a copper content of 37% (with a particle size of 2 to 150mm) (addition amount per hour) 10.55 tons, while adding 1.5 tons of anthracite, 10588N m 3 Oxygen-enriched air with an oxyg...
Embodiment 2
[0027] The composition of the copper concentrate used is:
[0028] the element
Cu(%)
Fe(%)
S(%)
SiO 2 (%)
As(%)
MgO+Al 2 o 3 (%)
content
24
19.8
23
11
0.3
2.7
[0029] The standard coal composition used as fuel is:
[0030] Element
Volatile matter
Ash
total
%
70.00
12.00
18.00
100.00
[0031] The batching is carried out according to the mass ratio of the copper content of the copper concentrate to the copper content of the waste miscellaneous copper = 1:0.4. In the smelting process of the horizontal oxygen bottom-blown furnace (furnace specification Φ3.1×11m), add 8 tons of copper concentrate and 3 tons of scrap copper scrap with copper content of 26% per hour, and add additional per hour 0.2 tons of anthracite, 2000N m 3 Oxygen-enriched air with an oxygen concentration of 90% and 0.1 tons of quartz stone (...
PUM
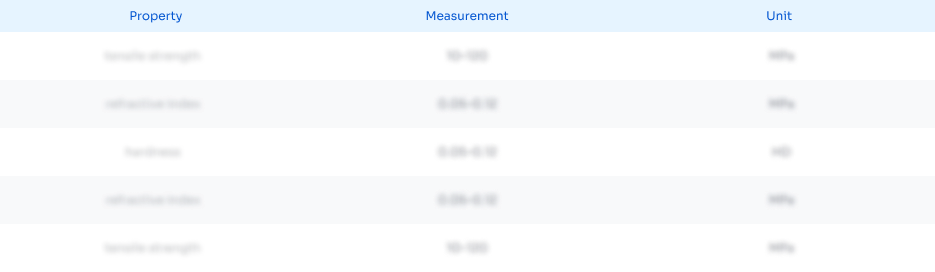
Abstract
Description
Claims
Application Information

- Generate Ideas
- Intellectual Property
- Life Sciences
- Materials
- Tech Scout
- Unparalleled Data Quality
- Higher Quality Content
- 60% Fewer Hallucinations
Browse by: Latest US Patents, China's latest patents, Technical Efficacy Thesaurus, Application Domain, Technology Topic, Popular Technical Reports.
© 2025 PatSnap. All rights reserved.Legal|Privacy policy|Modern Slavery Act Transparency Statement|Sitemap|About US| Contact US: help@patsnap.com