System and method for producing vanadium trioxide
A technology of vanadium trioxide and combustion system, applied in vanadium oxide and other directions, can solve the problems of low efficiency, inability to realize large-scale production, high production equipment and process, and achieve increased contact area, reliable heating method, and high production efficiency. Effect
- Summary
- Abstract
- Description
- Claims
- Application Information
AI Technical Summary
Problems solved by technology
Method used
Image
Examples
Embodiment 1
[0040] Example 1: With a feed rate of 300kg / h, the vanadium pentoxide powder enters Φ900×3500mm through the feed screw and feed leg as attached figure 1 The fluidized reduction furnace shown. After the coke oven gas is burned, flue gas at 1200°C is formed, and the flue gas enters the fluidized reduction furnace, and the fluidized reduction furnace is heated to 800°C through heat exchange. 160Nm 3 The coke oven gas per hour enters from the air funnel at the bottom of the fluidized reduction furnace, blows up the vanadium pentoxide powder, and reduces it for 5 minutes to obtain vanadium trioxide, then the vanadium trioxide passes through the discharge leg, fluidized The cooler uses nitrogen and cooling water as the cooling medium to cool the vanadium trioxide to 80°C, and then enters the product silo through the discharge screw. The reaction tail gas is combusted and discharged after being dusted by the bag filter, and the vanadium trioxide particles in the tail gas enter the...
Embodiment 2
[0042] Example 2: With a feed rate of 400kg / h, the ammonium vanadate powder enters Φ900×3500mm through the feed screw and the feed leg as attached figure 1 The fluidized reduction furnace shown. The flue gas at 1000°C is formed after the coke oven gas is burned, and the flue gas enters the fluidized reduction furnace, and the fluidized reduction furnace is heated to 700°C through heat exchange. 180Nm 3 The coal gas of the gas generator / h enters from the air hopper at the bottom of the fluidized reduction furnace, blows the ammonium vanadate powder, and reduces it for 10 minutes to obtain vanadium trioxide, and then the vanadium trioxide passes through the discharge leg, fluidized The cooler uses nitrogen and cooling water as the cooling medium to cool the vanadium trioxide to 100°C, and then enters the product silo through the discharge screw. The reaction tail gas is combusted and discharged after being dusted by the bag filter, and the vanadium trioxide particles in the t...
Embodiment 3
[0044] Example 3: With a feed rate of 200kg / h, the ammonium vanadate powder enters Φ900×3500mm through the feed screw and the feed leg as attached figure 1 The fluidized reduction furnace shown. The flue gas at 700°C is formed after the blast furnace gas is burned, and the flue gas enters the fluidized reduction furnace, and the fluidized reduction furnace is heated to 600°C through heat exchange. 90Nm 3 The carbon monoxide gas per hour enters from the air hopper at the bottom of the fluidized reduction furnace, blows up the ammonium vanadate powder, and reduces it for 30 minutes to obtain vanadium trioxide, then the vanadium trioxide passes through the discharge leg and the fluidized cooler At the same time, the vanadium trioxide is cooled to 50°C with nitrogen and cooling water as the cooling medium, and then enters the product silo through the discharge screw. The reaction tail gas is combusted and discharged after being dusted by the bag filter, and the vanadium trioxid...
PUM
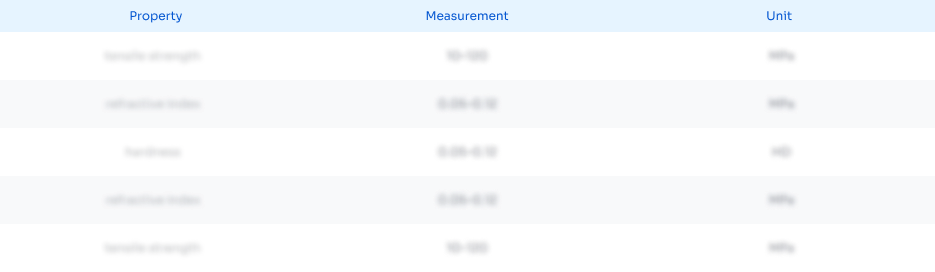
Abstract
Description
Claims
Application Information

- Generate Ideas
- Intellectual Property
- Life Sciences
- Materials
- Tech Scout
- Unparalleled Data Quality
- Higher Quality Content
- 60% Fewer Hallucinations
Browse by: Latest US Patents, China's latest patents, Technical Efficacy Thesaurus, Application Domain, Technology Topic, Popular Technical Reports.
© 2025 PatSnap. All rights reserved.Legal|Privacy policy|Modern Slavery Act Transparency Statement|Sitemap|About US| Contact US: help@patsnap.com