Method for preparing waterborne polyurethane taken as waterborne epoxy hardener
A water-based polyurethane and water-based epoxy technology, applied in the chemical industry, can solve the problems of complex synthesis of curing agent, difficulty in large-scale production, and difficult operation process, and achieve good curing epoxy resin system, easy operation, and improved compatibility Effect
- Summary
- Abstract
- Description
- Claims
- Application Information
AI Technical Summary
Problems solved by technology
Method used
Image
Examples
Embodiment 1
[0018] 1. Synthesis of the prepolymer containing terminal isocyanate groups: first add 20g isophorone diisocyanate (IPDI), 27.24 a mixture of 1,4-butanediol adipate (PBA-2000) and 13.62 g polyethylene glycol (PEG-1000), and dissolved in 15.87 (20%) g N-methylpyrrolidone (NMP) 2.38g (3%) of hydrophilic chain extender dimethylolpropionic acid (DMPA), stirred and heated to 80°C, added dropwise 0.2g (1%) dibutyl dilaurate (DBTDL), and Temperature controlled reaction for 3h.
[0019] 2. Neutralization and emulsification of the prepolymer: cool the prepared prepolymer to room temperature, then add 1.79g of triethylamine (TEA) for neutralization, react for 40 minutes, then add 152.2g of distilled water while vigorously stirring to emulsify it , to obtain an emulsion with a solid content of 30%.
[0020] 3. Amino-terminated water-based polyurethane emulsion: 5.4 g of ethylenediamine was added for chain extension (the molar ratio of amino group to isocyanate group was 2:1) and reacte...
Embodiment 2
[0027] 1. Synthesis of prepolymers containing terminal isocyanate groups: first add 20g hexamethylene diisocyanate (HDI), 20.44 A mixture of g poly-1,4-butylene adipate (PBA-2000) and 10.22 g of polyethylene glycol (PEG-1000), and dissolved in 18.93 g (25%) of N-methylpyrrolidone (NMP ) of 5.3g (7%) hydrophilic chain extender dimethylolpropionic acid (DMPA), stirred and heated to 90 ° C, dropwise added 0.8g (4%) dibutyl dilaurate (DBTDL), And temperature control reaction 4h.
[0028] 2. Neutralization and emulsification of the prepolymer: cool the prepared prepolymer to room temperature, then add 4.04g of triethylamine (TEA) for neutralization, react for 50 minutes, then add 112.83g of distilled water while vigorously stirring to emulsify it , to obtain an emulsion with a solid content of 35%.
[0029] 3. Amino-terminated water-based polyurethane emulsion: Add 7.2 g of ethylenediamine for chain extension (the molar ratio of amino group to isocyanate group is 3:1), and react ...
Embodiment 3
[0036] 1. Synthesis of the prepolymer containing terminal isocyanate groups: first add 20g isophorone diisocyanate (IPDI), 27.24 g polyadipate-1,4-butylene glycol (PBA-2000) and 13.62g polyethylene glycol (PEG-1000) mixture, and dissolved in 15.87g (20%) N-methylpyrrolidone (NMP ) of 2.38g (3%) hydrophilic chain extender dimethylol propionic acid (DMPA), stirred and heated to 100 ° C, dropwise added 0.4g (2%) dibutyl dilaurate (DBTDL), And temperature control reaction 5h.
[0037] 2. Neutralization and emulsification of the prepolymer: cool the prepared prepolymer to room temperature, then add 1.79g of triethylamine (TEA) for neutralization, react for 60 minutes, then add 138.61g of distilled water while vigorously stirring to emulsify it , to obtain an emulsion with a solid content of 32%.
[0038] 3. Amino-terminated aqueous polyurethane emulsion: add 6.18 g of diethylenetriamine for chain extension (the molar ratio of amino groups to isocyanate groups is 2:1), and react f...
PUM
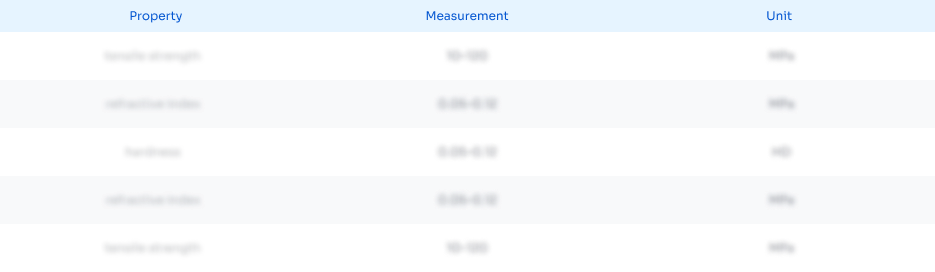
Abstract
Description
Claims
Application Information

- R&D
- Intellectual Property
- Life Sciences
- Materials
- Tech Scout
- Unparalleled Data Quality
- Higher Quality Content
- 60% Fewer Hallucinations
Browse by: Latest US Patents, China's latest patents, Technical Efficacy Thesaurus, Application Domain, Technology Topic, Popular Technical Reports.
© 2025 PatSnap. All rights reserved.Legal|Privacy policy|Modern Slavery Act Transparency Statement|Sitemap|About US| Contact US: help@patsnap.com