Resource recycling method of metallurgical flue gas
A technology of recycling and flue gas, which is applied in the field of energy chemistry, can solve the problem of insufficient use of heat and achieve the effect of reducing emissions
- Summary
- Abstract
- Description
- Claims
- Application Information
AI Technical Summary
Problems solved by technology
Method used
Image
Examples
specific Embodiment approach
[0019] DETAILED DESCRIPTION OF THE PREFERRED EMBODIMENTS The essence of the present invention will be further described with examples in conjunction with the accompanying drawings, but each example does not constitute a limitation to the present invention.
[0020] The specific implementation process is as follows: figure 1 with figure 2 First, the high-temperature metallurgical flue gas directly coming out of the metallurgical furnace passes through the "regenerator layer" of the cascaded regenerator after dedusting, followed by high-temperature regenerator (about 850°C)-medium-temperature regenerator (about 550°C)-low temperature Regenerator (about 250°C); the flue gas that has undergone heat exchange from the low-temperature regenerator passes through the desulfurization purification device to fully remove the acid gas in the flue gas; the flue gas after desulfurization is reversed to the deployment gas Through the catalytic "heat exchange layer" of the cascaded regenerat...
Embodiment 1
[0023] Flue gas composition of a copper smelter
[0024]
[0025] Catalytic material: Ni / Al 2 o 3
[0026] High temperature heat storage body: working temperature, 860°C; phase change heat storage material, Ni / Na 2 CO 3
[0027] Medium temperature heat storage body temperature: working temperature, 572°C; phase change heat storage material, Al / Al 2 o 3
[0028] Low temperature heat storage body temperature: working temperature, 265°C; phase change heat storage material, KCl+ZnCl 2
[0029] Outlet flue gas temperature: 260°C
[0030] Deployment gas: CH 4
[0031] CH 4 with CO 2 Conversion rate: 96%, 86%
[0032] Export flue gas composition
[0033]
Embodiment 2
[0035] Composition of flue gas during blast furnace smelting in a steel plant
[0036]
[0037] Catalytic material: Ni / Al 2 o 3
[0038] High temperature heat storage body: working temperature, 880°C; phase change heat storage material, Ni / Na 2 CO 3
[0039] Medium temperature heat storage body temperature: working temperature, 562°C; phase change heat storage material, Al / Al 2 o 3
[0040]Low temperature heat storage body temperature: working temperature, 245°C; phase change heat storage material, KCl+ZnCl 2
[0041] Deployment gas: CH 4 , O 2
[0042] CH 4 with CO 2 Conversion rates: 95%, 84%
[0043] Export flue gas composition
[0044]
PUM
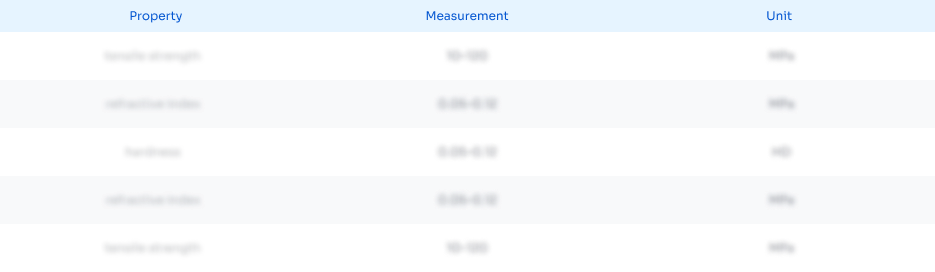
Abstract
Description
Claims
Application Information

- Generate Ideas
- Intellectual Property
- Life Sciences
- Materials
- Tech Scout
- Unparalleled Data Quality
- Higher Quality Content
- 60% Fewer Hallucinations
Browse by: Latest US Patents, China's latest patents, Technical Efficacy Thesaurus, Application Domain, Technology Topic, Popular Technical Reports.
© 2025 PatSnap. All rights reserved.Legal|Privacy policy|Modern Slavery Act Transparency Statement|Sitemap|About US| Contact US: help@patsnap.com