Desulfurization purification method of low-temperature sintering flue gas
A technology for low-temperature sintering and sintering flue gas, applied in chemical instruments and methods, separation methods, gas treatment, etc. The effect of low operating costs
- Summary
- Abstract
- Description
- Claims
- Application Information
AI Technical Summary
Problems solved by technology
Method used
Examples
Embodiment 1
[0023] A method for desulfurization and purification of low-temperature sintering flue gas, mainly comprising the following steps:
[0024] (1) The sintering flue gas from the sintering machine is first passed into the electrostatic precipitator for purification, and then drawn out by the exhaust fan through the flue, and is sent to the heat exchanger after switching between the flue gas bypass baffle valve and the inlet baffle valve Increase the temperature, and the temperature of the low-temperature sintering flue gas after heating rises to above 110°C;
[0025] (2) The heated sintering flue gas is passed into the reaction kettle through the pipeline, and ozone is passed into, so that the flue gas and ozone react;
[0026] (3) The oxidized flue gas enters the desulfurization tower through the pipeline, and the flue gas enters the flue gas distributor at the top of the desulfurization tower. After the air flow is uniform, it contacts and reacts with the desulfurizer atomized ...
Embodiment 2
[0030] A method for desulfurization and purification of low-temperature sintering flue gas, mainly comprising the following steps:
[0031] (1) The sintering flue gas from the sintering machine is first passed into the electrostatic precipitator for purification, and then drawn out by the exhaust fan through the flue, and is sent to the heat exchanger after switching between the flue gas bypass baffle valve and the inlet baffle valve Increase the temperature, and the temperature of the low-temperature sintering flue gas after heating rises to above 110°C;
[0032] (2) The heated sintering flue gas is passed into the reaction kettle through the pipeline, and ozone is passed into, so that the flue gas and ozone react;
[0033] (3) The oxidized flue gas enters the desulfurization tower through the pipeline, and the flue gas enters the flue gas distributor at the top of the desulfurization tower. After the air flow is uniform, it contacts and reacts with the desulfurizer atomized ...
Embodiment 3
[0039] A method for desulfurization and purification of low-temperature sintering flue gas, mainly comprising the following steps:
[0040] (1) The sintering flue gas from the sintering machine is first passed into the electrostatic precipitator for purification, and then drawn out by the exhaust fan through the flue, and is sent to the heat exchanger after switching between the flue gas bypass baffle valve and the inlet baffle valve Increase the temperature, and the temperature of the low-temperature sintering flue gas after heating rises to above 110°C;
[0041] (2) The heated sintering flue gas is passed into the reaction kettle through the pipeline, and ozone is passed into, so that the flue gas and ozone react;
[0042] (3) The oxidized flue gas enters the desulfurization tower through the pipeline, and the flue gas enters the flue gas distributor at the top of the desulfurization tower. After the air flow is uniform, it contacts and reacts with the desulfurizer atomized ...
PUM
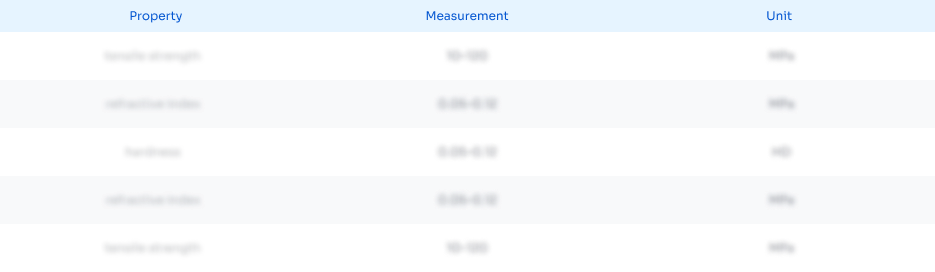
Abstract
Description
Claims
Application Information

- Generate Ideas
- Intellectual Property
- Life Sciences
- Materials
- Tech Scout
- Unparalleled Data Quality
- Higher Quality Content
- 60% Fewer Hallucinations
Browse by: Latest US Patents, China's latest patents, Technical Efficacy Thesaurus, Application Domain, Technology Topic, Popular Technical Reports.
© 2025 PatSnap. All rights reserved.Legal|Privacy policy|Modern Slavery Act Transparency Statement|Sitemap|About US| Contact US: help@patsnap.com