Emission reduction system of sintered fume nitric oxide with low energy consumption and method thereof
A technology of nitrogen oxides and sintering flue gas, which is applied in the direction of chemical instruments and methods, separation methods, and dispersed particle separation, can solve the problems of unfavorable nitrogen oxide removal efficiency, high operating cost, and low removal efficiency, and achieve Reduced denitrification costs, simple system, and the effect of reducing total emissions
- Summary
- Abstract
- Description
- Claims
- Application Information
AI Technical Summary
Problems solved by technology
Method used
Image
Examples
Embodiment Construction
[0044] The present invention will be described in detail below in conjunction with the accompanying drawings and embodiments.
[0045] see figure 1 , a low-energy sintering flue gas nitrogen oxide emission reduction system of the present invention is mainly composed of a circulating smoke hood 1, a circulating fan 2, a circulating flue gas dust collector 3, an air mixing valve 4, an air mixing regulating pipe 5, and a circulating pipe 6. Baffle valve 7, denitrification dust collector 8, denitrification device 9, dust collector 10, desulfurization device 11, main exhaust fan 12, exhaust chimney 13, wind box A for high nitrogen oxide concentration area and wind box B for low nitrogen oxide concentration area.
[0046] This system divides all the exhaust boxes in the lower part of the sintering machine trolley into high-concentration areas and low-concentration areas according to the concentration of nitrogen oxides. The denitrification and dust collector 8 is connected to the a...
PUM
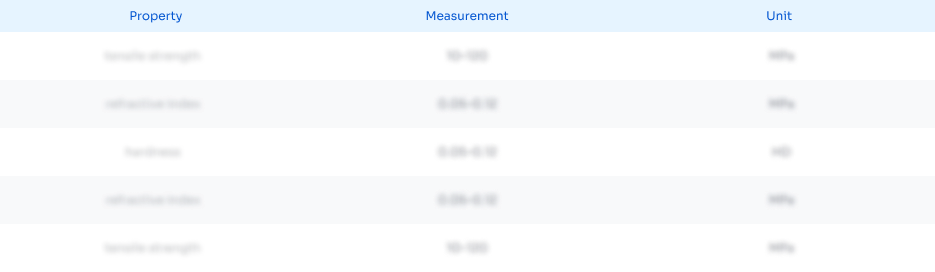
Abstract
Description
Claims
Application Information

- R&D
- Intellectual Property
- Life Sciences
- Materials
- Tech Scout
- Unparalleled Data Quality
- Higher Quality Content
- 60% Fewer Hallucinations
Browse by: Latest US Patents, China's latest patents, Technical Efficacy Thesaurus, Application Domain, Technology Topic, Popular Technical Reports.
© 2025 PatSnap. All rights reserved.Legal|Privacy policy|Modern Slavery Act Transparency Statement|Sitemap|About US| Contact US: help@patsnap.com