Process for extracting rare-earth from sulfuric acid treating phosphorite process
A sulfuric acid treatment and rare earth technology, which is applied in the direction of improving process efficiency and can solve the problems of low extraction efficiency of rare earth and difficult recovery of rare earth
- Summary
- Abstract
- Description
- Claims
- Application Information
AI Technical Summary
Problems solved by technology
Method used
Examples
Embodiment 1
[0023] 25%P 2 o 5 Crude phosphoric acid, containing 0.5g / L REO, is directly extracted by TBP (TBP and kerosene volume ratio 1:1), to obtain an organic phase and raffinate loaded with phosphoric acid, and the raffinate contains 10% P 2 o 5 and 0.5g / L REO.
[0024] Under the condition of 25°C, use 1.5M P204 (P204 and n-hexane volume ratio 1:1) to organically extract the raffinate acid, the extraction ratio is 1:1, countercurrent extraction is 20 stages, and the loaded rare earth organic phase and the secondary phase are obtained. raffinate. The rare earth-loaded organic phase was washed with 3M hydrochloric acid, the stripping ratio was O / A=1:10, and the rare earth chloride stripping liquid and blank organic phase were obtained through five stages of stripping. After adjusting the pH of the stripping solution to 3, add oxalic acid for precipitation according to 150% of the theoretical amount to obtain rare earth oxalate, which is calcined to obtain rare earth oxide. The yiel...
Embodiment 2
[0026] 30%P 2 o 5 Crude phosphoric acid, containing 0.15g / L REO, is directly extracted with a mixture of cyclohexanone and isopropyl ether to obtain an organic phase and raffinate loaded with phosphoric acid, and the raffinate contains 20% P 2 o 5 and 0.16g / L REO.
[0027] Under the condition of 30 ℃, use 1.5M P204 and TBP mixture (P204, TBP and kerosene volume ratio 0.8:0.2:1) to organically extract the raffinate acid, the extraction ratio is 1:1, countercurrent extraction is 18 stages, and the loaded Rare earth organic phase and secondary raffinate. The rare earth-loaded organic phase was washed with 3M hydrochloric acid, and the stripping ratio was O / A=20:1. After 20 stages of stripping, the rare earth chloride stripping solution and a blank organic phase were obtained. After adjusting the pH of the stripping solution to 2, potassium oxalate was added to precipitate according to 120% of the theoretical amount to obtain rare earth oxalate, which was calcined to obtain ra...
Embodiment 3
[0029] 35%P 2 o 5 Crude phosphoric acid, containing 1.8g / L REO, was directly extracted with a mixture of cyclohexanone, isopropyl ether and butanol to obtain an organic phase loaded with phosphoric acid and a raffinate containing 25% P 2 o 5 and 4.5g / L REO.
[0030] Under the condition of 40°C, use 2.0M (P204+P507) mixture (extractant and kerosene volume ratio 2:1) to organically extract the raffinate acid, the extraction ratio is 5:1, countercurrent extraction is 10 stages, and the loaded rare earth is obtained Organic phase and secondary raffinate. The rare earth-loaded organic phase was washed with 6M hydrochloric acid, and the stripping ratio was O / A=2:1. After 8 stages of stripping, the rare earth chloride stripping solution and a blank organic phase were obtained. After adjusting the pH of the stripping solution to 3, add ammonium oxalate for precipitation according to 150% of the theoretical amount to obtain rare earth oxalate, and calcinate to obtain rare earth oxi...
PUM
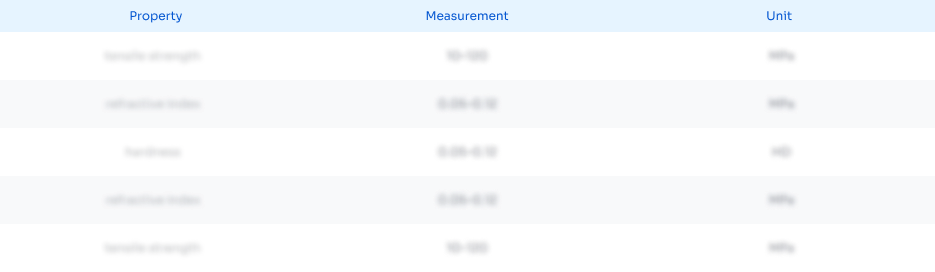
Abstract
Description
Claims
Application Information

- R&D
- Intellectual Property
- Life Sciences
- Materials
- Tech Scout
- Unparalleled Data Quality
- Higher Quality Content
- 60% Fewer Hallucinations
Browse by: Latest US Patents, China's latest patents, Technical Efficacy Thesaurus, Application Domain, Technology Topic, Popular Technical Reports.
© 2025 PatSnap. All rights reserved.Legal|Privacy policy|Modern Slavery Act Transparency Statement|Sitemap|About US| Contact US: help@patsnap.com