Method for preparing carbocoal by thermally cracking raw coal with external-heat horizontal rotary charring furnace
A rotary carbonization furnace and thermal cracking technology, applied in the field of coal chemical industry, can solve the problems of unreachable chemical utilization, affecting the quality of semi-coke, and shortage of raw materials, so as to reduce the generation of harmful gases, increase the usable value, and improve the utilization rate Effect
- Summary
- Abstract
- Description
- Claims
- Application Information
AI Technical Summary
Problems solved by technology
Method used
Image
Examples
Embodiment 1
[0023] 100kg of raw coal with a particle size of 20-25mm is sent to the drying section of the rotary carbonization furnace through a conveyor, where it is dried and desorbed at 260°C for 30 minutes to remove water and gas adsorbed in the pores. The dried raw coal enters the dry distillation section of the rotary carbonization furnace, and is thermally cracked at a material temperature of 600°C for 3 hours. After thermal cracking, blue charcoal, tar and coal gas are obtained. The pressure value of the rotary carbonization furnace is controlled at 10mm H 2 O, maintained between slightly negative pressure and slightly positive pressure. The installation method of the rotary carbonization furnace is horizontal, and the heating method of the rotary carbonization furnace is external heating. Part of the purified coal gas is sent to the combustion furnace to be fully combusted with hot air, and the generated hot air is sent into the jacket of the carbonization furnace dry distillation...
Embodiment 2
[0025] 80kg of raw coal with a particle size of 8-10mm is sent to the drying section of the rotary carbonization furnace through a conveyor, where it is dried and desorbed at 220°C for 20 minutes. The dried raw coal is sent to the dry distillation section of the rotary carbonization furnace, where it is thermally cracked at a material temperature of 650°C for 2.5 hours. After thermal cracking, blue charcoal, tar and coal gas are obtained. The pressure value is controlled at -10mm H 2 O. The blue char produced after cracking is sent to the coke quenching furnace for coke quenching, and is cooled by the countercurrent normal temperature nitrogen and the red hot red coke in the rotary dry quenching furnace. After quenching the coke, it enters the coke sieving device for screening treatment to obtain the finished blue charcoal. The mixture of high-temperature coal gas and tar produced after cracking is drawn from the gas guide pipe of the rotary carbonization furnace and enters th...
Embodiment 3
[0027] 120kg of raw coal with a particle size of 10-15mm is sent to the drying section of the rotary carbonization furnace through a conveyor, where it is dried and desorbed at 250°C for 60 minutes. The dried raw coal is sent to the dry distillation section of the rotary carbonization furnace, and is thermally cracked at a material temperature of 670°C for 4 hours. After thermal cracking, blue charcoal, tar and coal gas are obtained. The pressure value is controlled at 5mm H 2 O. The blue charcoal produced after cracking is sent to the coke oven for coke quenching, and the blue charcoal produced is sent to the cooler for cooling under the condition of isolating air, and the cooler adopts the form of circulating water spray cooling. After quenching the coke, it enters the coke sieving device for screening treatment to obtain the finished blue charcoal. The mixture of high-temperature coal gas and tar produced after cracking is drawn from the gas guide pipe of the rotary carboni...
PUM
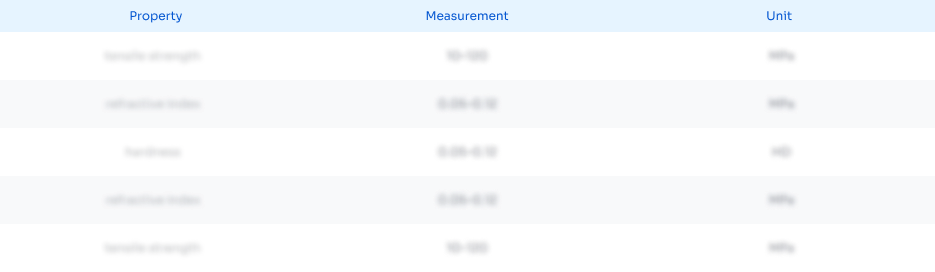
Abstract
Description
Claims
Application Information

- Generate Ideas
- Intellectual Property
- Life Sciences
- Materials
- Tech Scout
- Unparalleled Data Quality
- Higher Quality Content
- 60% Fewer Hallucinations
Browse by: Latest US Patents, China's latest patents, Technical Efficacy Thesaurus, Application Domain, Technology Topic, Popular Technical Reports.
© 2025 PatSnap. All rights reserved.Legal|Privacy policy|Modern Slavery Act Transparency Statement|Sitemap|About US| Contact US: help@patsnap.com