Preparation method of EVA sole bonding promoter
An adhesion promoter and reaction solvent technology, which is applied in the preparation of EVA sole adhesion promoters and the preparation of surface treatment agents, can solve problems such as being unsuitable for use in winter, easy to gel, and yellowing of the material surface, and achieves remarkable results. Adhesion promotion, good comprehensive performance and good affinity
- Summary
- Abstract
- Description
- Claims
- Application Information
AI Technical Summary
Problems solved by technology
Method used
Examples
Embodiment 1
[0031] 1200 grams of reaction solvent (components are toluene 50w%, ethyl acetate 10w%, methyl ethyl ketone 20w%, acetone 20w%) is added in the reactor that has stirring and reflux device, then drops into 100 grams of neoprene rubber and 30 grams Chlorinated polyethylene was stirred and the temperature was controlled to be 50°C. After the neoprene and chlorinated polyethylene are completely dissolved, fill the reactor with nitrogen, add 20 grams of methyl methacrylate and 30 grams of vinyl acetate, and add 1.2 grams of benzoyl peroxide to polymerize after heating up to 75°C reaction. After 2 hours of polymerization reaction, add 5 grams of acrylic acid, continue the reaction for 1 hour, then turn off the nitrogen gas, cool down to 30 ° C, then add 5 grams of vinyl resin and 1 gram of 2,6-di-tert-butyl p-cresol, stir well Discharging to obtain the graft copolymer.
[0032] 500 grams of graft copolymers are mixed with 750 grams of diluting solvent (components are toluene 50w%,...
Embodiment 2
[0034] 800 grams of reaction solvent (components are toluene 30w%, ethyl acetate 30w%, methyl ethyl ketone 10w%, acetone 30w%) is added in the reactor that has stirring and reflux device, then drops into 100 grams of neoprene rubber and 50 grams Chlorinated polyethylene was stirred and the temperature was controlled to be 70°C. After the neoprene and chlorinated polyethylene are completely dissolved, fill the reactor with nitrogen, add 30 grams of methyl methacrylate and 50 grams of vinyl acetate, and add 2.4 grams of benzoyl peroxide to polymerize after heating up to 90°C reaction. After 3 hours of polymerization reaction, add 10 grams of acrylic acid, continue the reaction for 2 hours, then turn off the nitrogen, cool down to 50 ° C, then add 10 grams of vinyl resin and 2 grams of 2,6-di-tert-butyl p-cresol, stir well Discharging to obtain the graft copolymer.
[0035] 500 grams of graft copolymers are mixed with 1500 grams of diluting solvent (components are toluene 20w%,...
Embodiment 3
[0037] 1000 grams of reaction solvent (components are toluene 40w%, ethyl acetate 10w%, methyl ethyl ketone 40w%, acetone 10w%) is added in the reactor that has stirring and reflux device, then drops into 100 grams of neoprene rubber and 40 grams Chlorinated polyethylene was stirred and the temperature was controlled to be 60°C. After the chloroprene rubber and chlorinated polyethylene are completely dissolved, fill the reactor with nitrogen, add 30 grams of methyl methacrylate and 40 grams of vinyl acetate, and add 1.8 grams of benzoyl peroxide to polymerize after heating up to 85°C reaction. After 2.5 hours of polymerization reaction, add 8 grams of acrylic acid, continue the reaction for 1.5 hours, turn off the nitrogen, cool down to 40 ° C, then add 8 grams of vinyl resin and 1.5 grams of 2,6-di-tert-butyl p-cresol, stir well Discharging to obtain the graft copolymer.
[0038] 500 grams of graft copolymers are mixed with 1000 grams of dilution solvent (component is tolue...
PUM
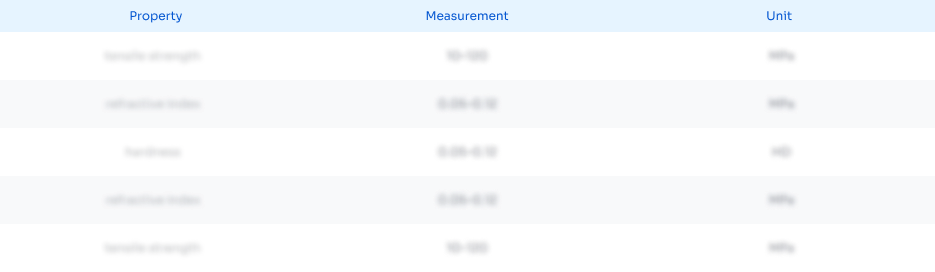
Abstract
Description
Claims
Application Information

- R&D Engineer
- R&D Manager
- IP Professional
- Industry Leading Data Capabilities
- Powerful AI technology
- Patent DNA Extraction
Browse by: Latest US Patents, China's latest patents, Technical Efficacy Thesaurus, Application Domain, Technology Topic, Popular Technical Reports.
© 2024 PatSnap. All rights reserved.Legal|Privacy policy|Modern Slavery Act Transparency Statement|Sitemap|About US| Contact US: help@patsnap.com