Automatic ball unloading device for 3M7780 grinder
A grinding machine and ball box technology, applied in the direction of grinding machines, spherical grinding machines, grinding/polishing equipment, etc., can solve the problems of reduced operating efficiency, reduced economic benefits, increased labor intensity, etc., and achieve the goal of improving the degree of automatic operation and benefit indicators Improve the effect of breakthrough, production and processing efficiency
- Summary
- Abstract
- Description
- Claims
- Application Information
AI Technical Summary
Problems solved by technology
Method used
Image
Examples
Embodiment Construction
[0008] Such as figure 1 Shown, the present invention comprises oil collection box 1, filter screen 5, oil pump 2, waits for material box 3, waits for ball box 4.
[0009] The above-mentioned oil collection tank 1 is filled with oil, and the middle part is provided with a filter screen 5 that separates the oil collection tank 1 into two cavities. The left cavity is provided with an oil pump 2, and the right cavity is provided with an equal material box 3, and an equal ball Two holes are arranged on the box 4, and two oil pipes are installed respectively, wherein one oil pipe is communicated with the oil pump 2, and the other oil pipe outlet is connected to the waiting material box 3.
[0010] When used, such as figure 2 As shown, the equal ball box 4 is installed between the dynamic and static grinding plates 6, 7 of the grinding machine when the balls are unloaded, pressurized by the machine tool, and the equal ball box 4 is firmly clamped therein. The oil pump 2 pumps the ...
PUM
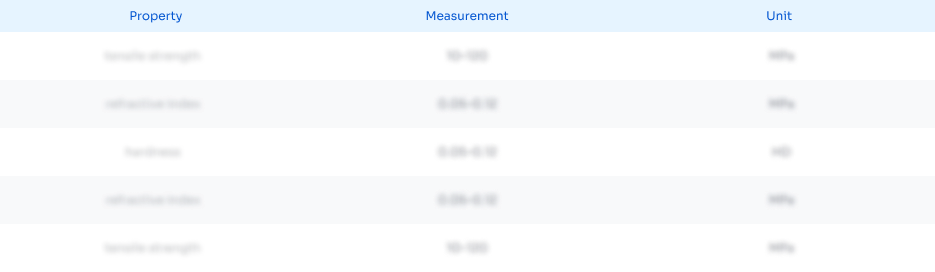
Abstract
Description
Claims
Application Information

- R&D
- Intellectual Property
- Life Sciences
- Materials
- Tech Scout
- Unparalleled Data Quality
- Higher Quality Content
- 60% Fewer Hallucinations
Browse by: Latest US Patents, China's latest patents, Technical Efficacy Thesaurus, Application Domain, Technology Topic, Popular Technical Reports.
© 2025 PatSnap. All rights reserved.Legal|Privacy policy|Modern Slavery Act Transparency Statement|Sitemap|About US| Contact US: help@patsnap.com