Method for preparing back point contact structure of crystalline silicon solar cell
A contact structure, solar cell technology, applied in circuits, electrical components, semiconductor devices, etc., can solve problems such as harsh power requirements, low production efficiency, distorted substrate silicon wafer lattice structure, etc. low cost effect
- Summary
- Abstract
- Description
- Claims
- Application Information
AI Technical Summary
Problems solved by technology
Method used
Image
Examples
Embodiment Construction
[0023] Below in conjunction with accompanying drawing, specific implementation method of the present invention is described in further detail:
[0024] Such as figure 1 As shown, the upper surface of a crystalline silicon solar cell is a cell substrate 1 with a textured structure and a metal grid line 2 on the upper surface, and a passivation film 3 and an aluminum back electrode 4 are deposited on the back surface.
[0025] The preparation process of the back point contact structure of the crystalline silicon solar cell involved in the present invention is as follows:
[0026] 1. According to the required crystalline silicon solar cell structure, determine the style of the cell back point contact structure, that is, the density of the point array and the size of the conductive contact point. The size of the contact point is usually 0.1-0.2mm, and the dot pitch is about 2mm, and the stencil for screen printing is made according to this pattern.
[0027] 2. Print the dot arra...
PUM
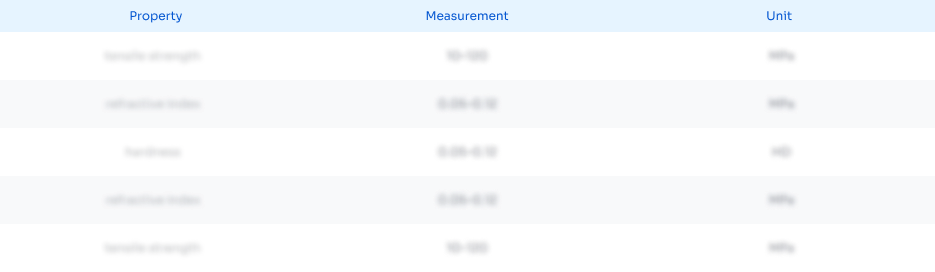
Abstract
Description
Claims
Application Information

- R&D Engineer
- R&D Manager
- IP Professional
- Industry Leading Data Capabilities
- Powerful AI technology
- Patent DNA Extraction
Browse by: Latest US Patents, China's latest patents, Technical Efficacy Thesaurus, Application Domain, Technology Topic, Popular Technical Reports.
© 2024 PatSnap. All rights reserved.Legal|Privacy policy|Modern Slavery Act Transparency Statement|Sitemap|About US| Contact US: help@patsnap.com