Process for washing, pre-desulfurizing and refining tapping steel slag of converter
A technology of tapping slag and pre-desulfurization, applied in the direction of manufacturing converters, etc., can solve the problems of non-desulfurization process research, heavy refining tasks, and reducing the sulfur content of the LF furnace to the station, so as to achieve simple operation, convenient large-scale production, and relieve pressure. Effect
- Summary
- Abstract
- Description
- Claims
- Application Information
AI Technical Summary
Problems solved by technology
Method used
Examples
Embodiment 1
[0018] The steel type is resistant to HIC X65, and the process of the present invention is used for converter tapping slag washing and pre-desulfurization: 100 tons of converter tapping, the tapping temperature is 1700 ° C, and aluminum and iron are used for strong deoxidation when tapping for 1.5 minutes, and the amount of aluminum and iron added is 4.5kg / t Steel; add synthetic slag at the bottom of the ladle before tapping, the addition amount is 8kg / t steel; use alloy chute for 2 minutes of tapping, add lime continuously and uniformly with the steel flow, the total addition amount is 6kg / t steel, before the end of tapping The addition is completed; the bottom blowing effect of the ladle is maintained during the tapping process, and the flow rate of the bottom blowing argon is controlled at 3NL / (min t); after tapping, aluminum particles are added to the slag surface of the ladle to deoxidize the slag surface, and the addition amount is 0.8kg / t Steel; slag washing ends steel s...
Embodiment 2
[0020] Steel type X70, using the process of the present invention to carry out converter tapping slag washing and pre-desulfurization: 100 tons of converter tapping, tapping temperature 1720°C, aluminum-iron strong deoxidation is used for 1.5 minutes of tapping, and the addition of aluminum and iron is 5kg / t steel; Add synthetic slag at the bottom of the ladle before steel, the addition amount is 5kg / t steel; use alloy chute when tapping for 2 minutes, add lime continuously and evenly with the steel flow, the total addition amount is 4kg / t steel, and add before the end of tapping; During the tapping process, the bottom blowing effect of the ladle is maintained, and the flow rate of the bottom blowing argon gas is controlled at 4NL / (min·t); at the end of tapping, aluminum particles are added to the slag surface of the ladle to deoxidize the slag surface, and the addition amount is 0.6kg / t steel; Oxidability of steel slag after washing: (FeO+MnO)≤3.1%, slag performance index (wei...
PUM
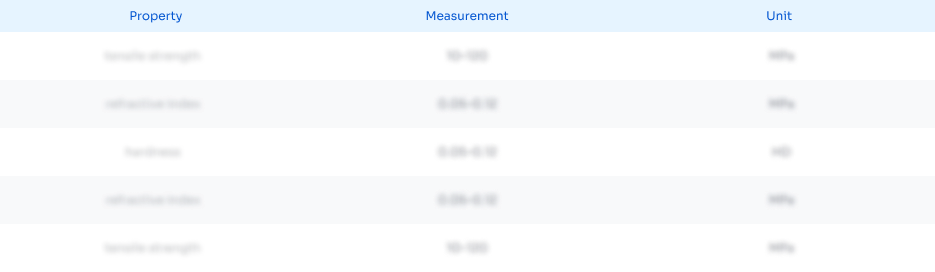
Abstract
Description
Claims
Application Information

- Generate Ideas
- Intellectual Property
- Life Sciences
- Materials
- Tech Scout
- Unparalleled Data Quality
- Higher Quality Content
- 60% Fewer Hallucinations
Browse by: Latest US Patents, China's latest patents, Technical Efficacy Thesaurus, Application Domain, Technology Topic, Popular Technical Reports.
© 2025 PatSnap. All rights reserved.Legal|Privacy policy|Modern Slavery Act Transparency Statement|Sitemap|About US| Contact US: help@patsnap.com