Production technology of poly (p-phenytene terephthalamide) resin
A technology of poly-p-phenylene terephthalamide and terephthaloyl chloride is applied in the field of preparing poly-p-phenylene terephthalamide resin, and can solve the requirements of particle size, extremely high environmental humidity, and high operating environment. Unfriendly and other problems, to avoid adverse effects, increase product molecular weight, and reduce costs
- Summary
- Abstract
- Description
- Claims
- Application Information
AI Technical Summary
Problems solved by technology
Method used
Examples
Embodiment 1
[0033] A kind of production technology of PPTA resin, specifically as follows: in the stainless steel reactor that 250L has jacket, inject and be dissolved with 7% calcium chloride (CaCl 2 ) 200 kg of N-methylpyrrolidone (NMP) solution, add 8.020 kg of p-phenylenediamine (PPDA) at 15 °C to fully dissolve it, and make NMP-CaCl 2- After the PPDA solution, cool to -15°C, slowly add 12.060 kg of terephthaloyl chloride (TPC), and react for 20 minutes to form a prepolymer; the -10°C prepolymer and 50wt% NMP-TPC solution were respectively Simultaneously pump 1000g / min and 27.40g / min into a counter-rotating twin-screw extruder with a diameter of φ50, an aspect ratio of 15, and a rotational speed of 200rpm, and control the precondensation reaction temperature at 15-25°C. After extruding into a co-rotating twin-screw extruder with a diameter of φ65, an aspect ratio of 50, and a rotational speed of 90rpm for polycondensation, the temperature of the co-rotating twin-screw extruder is cont...
Embodiment 2
[0035] A kind of production technology of PPTA resin, specifically as follows: in the stainless steel reactor that 250L has jacket, inject and be dissolved with 7% calcium chloride (CaCl 2 ) 200 kg of N-methylpyrrolidone (NMP) solution, add 8.020 kg of p-phenylenediamine (PPDA) at 15 °C to fully dissolve it, and make NMP-CaCl 2 - After the PPDA solution, cool to -15°C, slowly add 7.575 kg of terephthaloyl chloride (TPC), react for 20 minutes to form a prepolymer, continue to reduce the temperature of the reaction material to -10°C, and mix the prepolymer and The NMP-TPC solution of 50wt% is pumped into the diameter simultaneously with 898.3g / min and 62.5g / min respectively and is that phi 50, aspect ratio is 15, and rotating speed is to carry out pre-condensation reaction in the counter-rotating twin-screw extruder of 200rpm, control pre-condensation The polycondensation reaction temperature is 15-25°C. After high-speed mixing and pre-condensation, it is extruded into a co-rota...
Embodiment 3
[0037] In a 250L jacketed stainless steel reactor, inject 7% calcium chloride (CaCl 2 ) 200 kg of N-methylpyrrolidone (NMP) solution, add 8.020 kg of p-phenylenediamine (PPDA) at 15 °C to fully dissolve it, and make NMP-CaCl 2 After -PPDA solution, cool to -15°C, slowly add 12.060 kg of terephthaloyl chloride (TPC), react for 20 minutes to form a prepolymer, continue to reduce the temperature of the reaction material to -10°C, and mix the prepolymer and The TPC solution is simultaneously pumped at 1000g / min and 13.5g / min respectively into a counter-rotating twin-screw extruder with a diameter of φ50, an aspect ratio of 15, and a rotational speed of 200rpm. After mixing and precondensation, extrude into a co-rotating intermeshing twin-screw extruder with a diameter of φ65, an aspect ratio of 50, and a rotational speed of 90 rpm. The middle section of the intermeshing twin-screw extruder and the machine head are installed with an exhaust barrel filled with fillers at a height o...
PUM
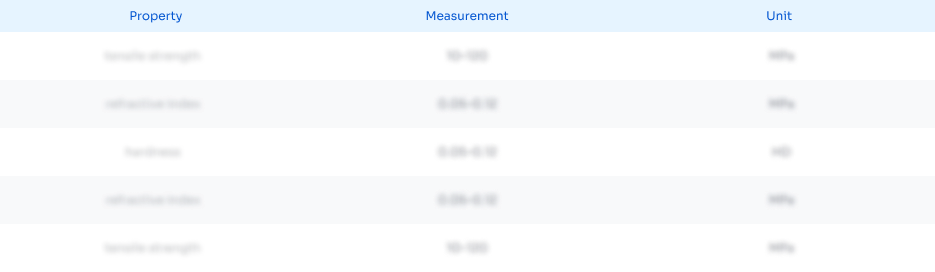
Abstract
Description
Claims
Application Information

- R&D Engineer
- R&D Manager
- IP Professional
- Industry Leading Data Capabilities
- Powerful AI technology
- Patent DNA Extraction
Browse by: Latest US Patents, China's latest patents, Technical Efficacy Thesaurus, Application Domain, Technology Topic, Popular Technical Reports.
© 2024 PatSnap. All rights reserved.Legal|Privacy policy|Modern Slavery Act Transparency Statement|Sitemap|About US| Contact US: help@patsnap.com