Filter material for biological aerated filter and preparation method thereof
A biological aerated filter and filter material technology, applied in the direction of sustainable biological treatment, chemical instruments and methods, biological water/sewage treatment, etc., can solve the problem of poor control of the amount of dosing, and achieve the benefit of microbial attachment and growth , Huge specific surface area, the effect of avoiding secondary pollution
- Summary
- Abstract
- Description
- Claims
- Application Information
AI Technical Summary
Problems solved by technology
Method used
Examples
Embodiment 1
[0016] Take 10kg of sewage treatment plant sludge into an oven at 105°C for 24h drying, ball mill it through a 100-mesh sieve, and take it out for use; take 80kg of sewage treatment plant sludge into an oven at 105°C and dry it for 24h, then ball-mill it through a 100-mesh sieve. Stir the sieved water plant sludge, sewage treatment plant sludge, 3kg coal powder and 7kg water glass thoroughly, and sprinkle water to form a raw material ball; put the molded raw material ball in an oven at 105°C for 24h; dry it The ready raw material balls are taken out, put into a box-type resistance furnace, heated to 450°C, and kept for 10 minutes for preheating. The preheated raw material balls are quickly moved into a program-controlled electric furnace that has been heated to 1000° C. and roasted for 60 minutes, then taken out, and cooled to room temperature to obtain the required filter material for the aerated biological filter.
[0017] Take BAF process water quality: BOD 5 The concentration...
Embodiment 2
[0019] Take 15kg of sewage treatment plant sludge into an oven at 105°C for 24h drying, ball mill through a 100-mesh sieve, and take it out for use; take 70kg of sewage treatment plant sludge into an oven at 105°C and dry it for 24h, then ball-mill it through a 100-mesh sieve. Stir the sieved water plant sludge, sewage treatment plant sludge, 5kg starch and 10kg water glass thoroughly, sprinkle water to form a raw material ball; put the molded raw material ball in an oven at 105°C for 24h; dry it well The raw material balls that have been prepared are taken out, placed in a box-type resistance furnace, heated to 500°C, and kept for 20 minutes for preheating. The pre-heated raw material balls are quickly moved into a program-controlled electric furnace that has been heated to 1100°C and roasted for 50 minutes, then taken out, and cooled to room temperature to obtain the required filter material for the aerated biological filter.
[0020] Take BAF process water quality: BOD 5 The c...
Embodiment 3
[0022] Take 20kg of sewage treatment plant sludge and put it in an oven at 105°C for 24h drying, ball mill it through a 100-mesh sieve, and take it out for use; take 60kg of sewage treatment plant sludge into an oven at 105°C and dry it for 24h, then ball-mill it through a 100-mesh sieve. Stir the sieved water plant sludge, sewage treatment plant sludge, 5kg sawdust and 15kg water glass thoroughly, and sprinkle water to form a raw material ball; put the molded raw material ball in an oven at 105°C and dry for 24h; The ready raw material balls are taken out, put into a box-type resistance furnace, heated to 550°C, and kept for 30 minutes for preheating. The preheated raw material balls are quickly moved into a program-controlled electric furnace that has been heated to 1200°C and roasted for 40 minutes, then taken out, and cooled to room temperature to obtain the required filter material for the aerated biological filter.
[0023] Take BAF process water quality: BOD 5 The concentr...
PUM
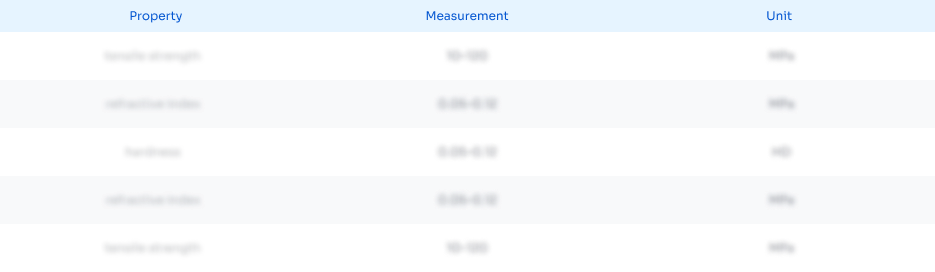
Abstract
Description
Claims
Application Information

- R&D
- Intellectual Property
- Life Sciences
- Materials
- Tech Scout
- Unparalleled Data Quality
- Higher Quality Content
- 60% Fewer Hallucinations
Browse by: Latest US Patents, China's latest patents, Technical Efficacy Thesaurus, Application Domain, Technology Topic, Popular Technical Reports.
© 2025 PatSnap. All rights reserved.Legal|Privacy policy|Modern Slavery Act Transparency Statement|Sitemap|About US| Contact US: help@patsnap.com