Manufacturing method of solder ring component for magnetron cathode assembly
A magnetron cathode and manufacturing method technology, applied in cold cathode manufacturing, discharge tube/lamp manufacturing, electrode system manufacturing, etc., can solve the problems of complex process, poor operability, high cost, etc., achieve simplified preparation process, and improve finished product The effect of improving production efficiency and yield
- Summary
- Abstract
- Description
- Claims
- Application Information
AI Technical Summary
Problems solved by technology
Method used
Image
Examples
example 1
[0028] An appropriate amount of Mo powder and Ru powder were ground in a high-energy ball mill for 25 hours to obtain evenly distributed solder powder. Mix the solder powder with a small amount of organic matter, such as terpineol and ethyl cellulose, to obtain a solder paste with certain fluidity. Automatic grouting device and image 3 The movement form of the needle relative to the molybdenum end cap shown in , accurately, uniformly and efficiently coats the solder paste on the groove of the molybdenum end cap, and forms a regular ring shape. Then, degrease and sinter the molybdenum end cap coated with solder paste in a hydrogen atmosphere furnace. The heating rate in the range of 150-550°C is 1.5°C / min, and the maximum sintering temperature is 1650°C, finally forming a solder ring part in the molybdenum end cap.
example 2
[0030] An appropriate amount of Mo powder, Ru powder and Ni powder were ground in a high-energy ball mill for 15 hours to obtain evenly distributed solder powder. Mix the solder powder with a small amount of organic matter, such as rosin, ethyl cellulose and paraffin wax emulsion, to obtain a solder paste with certain fluidity. Automatic grouting device and Figure 5 The movement form of the needle relative to the molybdenum end cap shown in , accurately, uniformly and efficiently coats the solder paste on the groove of the molybdenum end cap, and forms a regular ring shape. Then, the molybdenum end cap coated with solder paste is degreased in a furnace with a nitrogen atmosphere, and sintered in a furnace with a hydrogen atmosphere. The heating rate is 1°C / min in the range of 150-550°C, and the highest sintering temperature is 1450°C, finally forming a solder ring part in the molybdenum end cap.
example 3
[0032] An appropriate amount of Mo powder, Fe powder and Ni powder were ground in a roller mill for 10 h to obtain evenly distributed solder powder. Mix the solder powder with a small amount of organic matter, such as rosin, hydrogenated castor oil and paraffin emulsion, to obtain a solder paste with certain fluidity. Automatic grouting device and Figure 7 The movement form of the needle relative to the molybdenum end cap shown in , accurately, uniformly and efficiently coats the solder paste on the groove of the molybdenum end cap, and forms a regular ring shape. Then, the molybdenum end cap coated with solder paste is degreased in a furnace with an argon atmosphere, and sintered in a furnace with a hydrogen atmosphere. The heating rate is 2°C / min in the range of 150-550°C, and the maximum sintering temperature is 1100°C, finally forming a solder ring part in the molybdenum end cap.
PUM
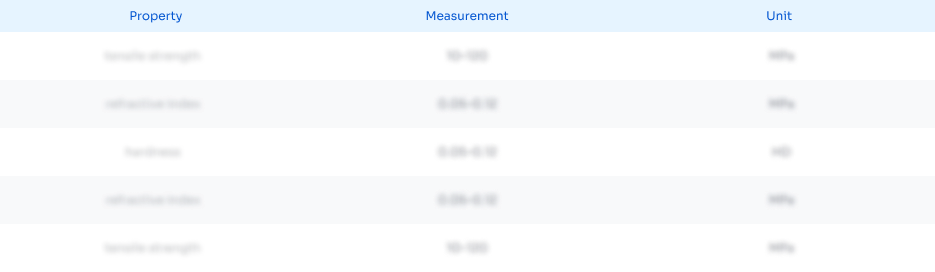
Abstract
Description
Claims
Application Information

- R&D Engineer
- R&D Manager
- IP Professional
- Industry Leading Data Capabilities
- Powerful AI technology
- Patent DNA Extraction
Browse by: Latest US Patents, China's latest patents, Technical Efficacy Thesaurus, Application Domain, Technology Topic, Popular Technical Reports.
© 2024 PatSnap. All rights reserved.Legal|Privacy policy|Modern Slavery Act Transparency Statement|Sitemap|About US| Contact US: help@patsnap.com