Forming technology for forging seamless steel pipe with large diameter and extra thick wall under ultrahigh pressure
A technology of seamless steel pipe and forming process, applied in the direction of manufacturing tools, metal processing equipment, forging/pressing/hammer devices, etc. Volume reduction, elimination of unequal wall thicknesses, and reduction of gross-to-net ratio
- Summary
- Abstract
- Description
- Claims
- Application Information
AI Technical Summary
Problems solved by technology
Method used
Examples
Embodiment Construction
[0015] Now the whole process of new molding technique of the present invention and forging forging is described as follows:
[0016] Step 1: Steel ingot pressing pliers handle, chamfering, chopping nozzle;
[0017] Step 2: Ingot drawing and cutting;
[0018] Step 3: blank upsetting;
[0019] Step 4: punching;
[0020] Step five: reaming;
[0021] Step 6: Use the mandrel and anvil with the same slope to pull the forging into a long tube with the same wall thickness and the same inner and outer taper;
[0022] Step 7: Withdraw the mandrel, and use the method of drawing without mandrel to pull the forging to size.
[0023] First of all, the same as the existing process, the steel ingot is clamped, chamfered, cut the nozzle, drawn and cut, and then punched with a punch, and the hole is expanded on the horse frame. Following technological process is key part of the present invention, now be described in detail as follows:
[0024] After reaming on the horse frame, with the co...
PUM
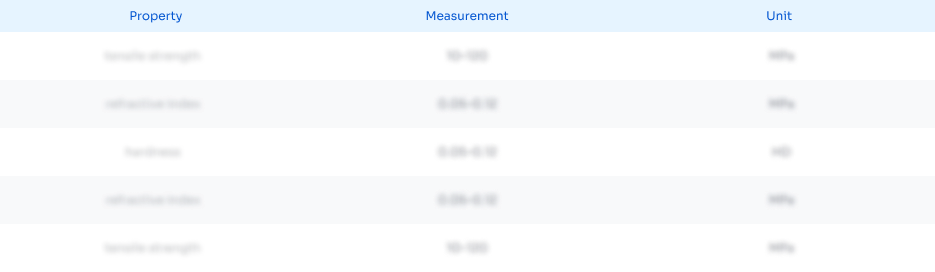
Abstract
Description
Claims
Application Information

- R&D
- Intellectual Property
- Life Sciences
- Materials
- Tech Scout
- Unparalleled Data Quality
- Higher Quality Content
- 60% Fewer Hallucinations
Browse by: Latest US Patents, China's latest patents, Technical Efficacy Thesaurus, Application Domain, Technology Topic, Popular Technical Reports.
© 2025 PatSnap. All rights reserved.Legal|Privacy policy|Modern Slavery Act Transparency Statement|Sitemap|About US| Contact US: help@patsnap.com