Method for modifying lignite
A technology of upgrading and lignite, which is applied in the petroleum industry, liquid carbon-containing fuels, fuels, etc., and can solve the problems of poor slurrying performance and low calorific value of lignite
- Summary
- Abstract
- Description
- Claims
- Application Information
AI Technical Summary
Problems solved by technology
Method used
Image
Examples
Embodiment 1
[0038] as attached figure 1 As shown, the raw material lignite is made into coal-water slurry by crusher and coal mill, and the coal-water slurry is sent to the loop reactor after being pressurized. The raw material coal-water slurry is sent into the casing, and the hot coal slurry after reaction is sent into the inner tube for heat exchange. In order to further increase the temperature of the coal slurry, an electromagnetic heater is installed outside the front end of the loop reactor, and the coal water slurry stays in the loop reactor for 15 to 35 minutes. The conditions depend on the properties of the lignite and the particle size of the coal-water slurry) After the reaction, the hot coal slurry enters the inner tube of the loop heat exchanger, and the temperature drops below 100°C and enters the settling tank. Add the settling agent into the settling tank, the clear water in the upper layer of the settling tank is sent to the coal mill, and the coal water slurry with hig...
Embodiment 2
[0040] as attached figure 2 As shown, the raw material lignite is made into coal-water slurry by crusher and coal mill, and the coal-water slurry is sent to the loop reactor after being pressurized, and a direct-connected loop heat exchanger without casing is installed in front of the loop reactor , using electromagnetic heating to heat the coal-water slurry to the reaction temperature. The coal-water slurry stays in the loop reactor for 15-35 minutes, and the hot coal slurry after reaction enters the loop reactor at a pressure of 6.0-12.0MPa and a temperature of 200-320°C (operating conditions depend on the properties of the lignite and the particle size of the coal-water slurry). The inner tube of the tube heat exchanger and the coolant of the ring tube heat exchanger are boiler feed water and cooling water. In the ring tube heat exchanger, the boiler water is heated and then sent to the steam drum to generate steam. The coal water slurry cooled by the boiler water Then it...
Embodiment 3
[0042] as attached image 3 As shown, the raw material lignite is made into coal-water slurry by crusher and coal mill, and the coal-water slurry is sent to the loop reactor after being pressurized. The raw material coal-water slurry is sent into the casing, and the hot coal slurry after reaction is sent into the inner tube for heat exchange. In order to further increase the temperature of the coal slurry, an electromagnetic heater is installed outside the front end of the loop reactor to heat the coal-water slurry to the reaction temperature. The coal-water slurry stays in the loop reactor for 15-35 minutes at a pressure of 6.0-12.0MPa and a temperature of 200-320°C (the operating conditions depend on the properties of the lignite and the particle size of the coal-water slurry). After the reaction, the hot coal slurry enters the inner tube of the loop heat exchanger, the temperature drops below 100°C and enters the settling tank, and the settling agent is added to the settli...
PUM
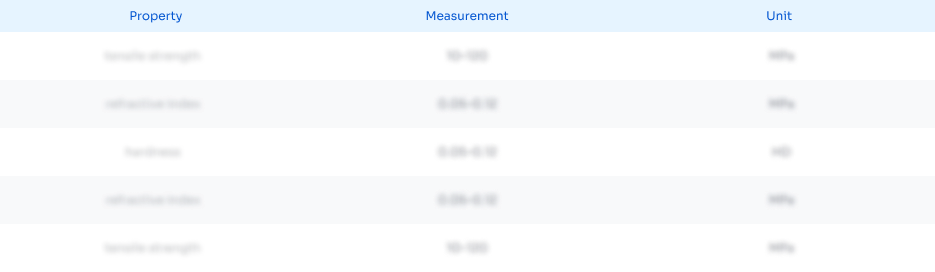
Abstract
Description
Claims
Application Information

- R&D Engineer
- R&D Manager
- IP Professional
- Industry Leading Data Capabilities
- Powerful AI technology
- Patent DNA Extraction
Browse by: Latest US Patents, China's latest patents, Technical Efficacy Thesaurus, Application Domain, Technology Topic, Popular Technical Reports.
© 2024 PatSnap. All rights reserved.Legal|Privacy policy|Modern Slavery Act Transparency Statement|Sitemap|About US| Contact US: help@patsnap.com