Method for manufacturing silicon nano structure
A technology of silicon nano and silicon dioxide, which is applied in nanostructure manufacturing, nanotechnology, nanotechnology, etc., can solve the problems of poor etch resistance, inability to mask, weaken PMMA's etch resistance, and achieve etch resistance Enhanced, tightly packed, smooth-edged effects
- Summary
- Abstract
- Description
- Claims
- Application Information
AI Technical Summary
Problems solved by technology
Method used
Image
Examples
Embodiment Construction
[0037] In order to make the object, technical solution and advantages of the present invention clearer, the present invention will be described in further detail below in conjunction with specific embodiments and with reference to the accompanying drawings.
[0038] The present invention utilizes PMMA positive electron beam glue to become negative electron beam glue when the incident electron beam dose is high enough and secondary electron beam irradiation to enhance the characteristics of PMMA etching resistance, so that the PMMA glue that plays a masking effect on the pattern resists The etching performance is greatly enhanced, and the preparation of silicon nanostructures is completed after dry etching.
[0039] Such as figure 1 as shown, figure 1 It is a flow chart of a method for preparing a silicon nanostructure provided by the present invention, the method comprising:
[0040] Step 1: making the layout required for electron beam exposure;
[0041] Step 2: Cleaning an...
PUM
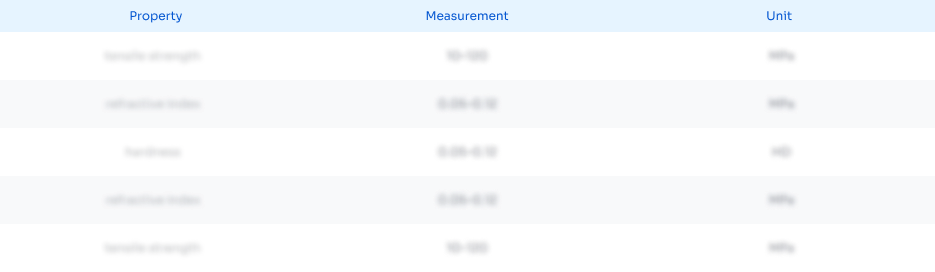
Abstract
Description
Claims
Application Information

- R&D
- Intellectual Property
- Life Sciences
- Materials
- Tech Scout
- Unparalleled Data Quality
- Higher Quality Content
- 60% Fewer Hallucinations
Browse by: Latest US Patents, China's latest patents, Technical Efficacy Thesaurus, Application Domain, Technology Topic, Popular Technical Reports.
© 2025 PatSnap. All rights reserved.Legal|Privacy policy|Modern Slavery Act Transparency Statement|Sitemap|About US| Contact US: help@patsnap.com