Electroplating technology for bearing quaternary alloy
A quaternary alloy and electroplating technology, which is applied to bearing components, shafts and bearings, mechanical equipment, etc., can solve problems such as inability to meet performance requirements, and achieve the effects of improving wear resistance, service life and carrying capacity
- Summary
- Abstract
- Description
- Claims
- Application Information
AI Technical Summary
Problems solved by technology
Method used
Examples
Embodiment 1
[0078] A bearing bush quaternary alloy electroplating process, comprising the following steps:
[0079] 1) Ultrasonic degreasing
[0080] Use trichlorethylene or hydrocarbon as the degreasing agent and use an ultrasonic cleaning machine to clean the oil, iron filings and other pollutants on the surface of the bearing bush. The cleaning time is 10-15 minutes, and the temperature of the degreasing agent is 50-60°C;
[0081] 2) Chemical degreasing
[0082] Use FD-211C degreasing powder for chemical degreasing, the concentration is 30-50g / L, the time is 3-5 minutes, and the temperature is 50-70°C; to remove the oil remaining in the pores, the product after degreasing can be Tested by water test method;
[0083] 3) Two-stage cleaning
[0084] Use urban countercurrent rinsing, and change the clean water every shift;
[0085] 4) Electrochemical degreasing
[0086] Use copper-lead powder material FD~318 electrolytic degreasing powder for degreasing, the concentration is 50-70g / L,...
PUM
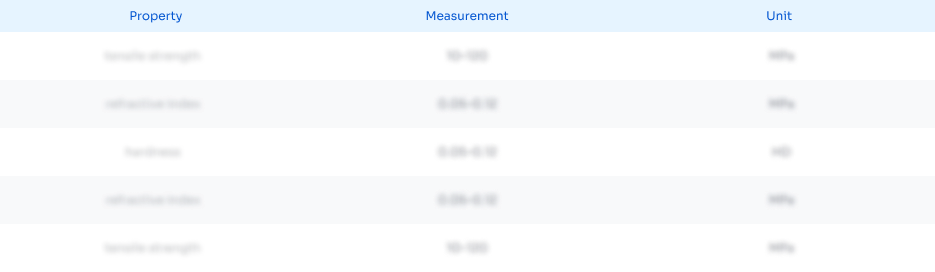
Abstract
Description
Claims
Application Information

- R&D
- Intellectual Property
- Life Sciences
- Materials
- Tech Scout
- Unparalleled Data Quality
- Higher Quality Content
- 60% Fewer Hallucinations
Browse by: Latest US Patents, China's latest patents, Technical Efficacy Thesaurus, Application Domain, Technology Topic, Popular Technical Reports.
© 2025 PatSnap. All rights reserved.Legal|Privacy policy|Modern Slavery Act Transparency Statement|Sitemap|About US| Contact US: help@patsnap.com